Dans l’environnement industriel concurrentiel actuel, la maîtrise de l’OEE (Efficacité Globale des Équipements), ou TRS (Taux de Rendement Synthétique), est indispensable. Ce critère de performance clé est essentiel pour les usines cherchant à maximiser leur efficacité de production. En combinant les indicateurs de disponibilité, de performance et de qualité, l’OEE fournit une mesure complète de la productivité, reflétant la véritable utilisation des équipements.
Cette métrique permet non seulement d’identifier où et comment les pertes se produisent dans le processus de production, mais aussi de définir des pistes d’amélioration concrètes. Dans ce contexte, comprendre et optimiser l’OEE devient un levier stratégique pour accroître la productivité et la rentabilité des installations industrielles.
Dans cet article, nous aborderons la signification et l’importance de l’OEE/TRS dans le cadre industriel, en expliquant comment il peut être calculé, analysé et utilisé pour piloter l’amélioration continue des processus de fabrication.
Compréhension de l’OEE et du TRS et du calcul
L’OEE (Efficacité Globale des Équipements) ou TRS (Taux de Rendement Synthétique) est un indicateur de performance crucial pour toute usine visant l’excellence opérationnelle. Sa capacité à fournir un aperçu détaillé de la performance de production rend cet indicateur indispensable pour le secteur industriel. Pourtant, sa compréhension et son application correctes restent un défi pour de nombreuses organisations.
Définitions et Composants
L’OEE est la multiplication de trois composants principaux : la Disponibilité, la Performance et la Qualité. Chacun de ces composants aborde un aspect différent de la performance de production :
- Disponibilité : mesure le pourcentage de temps prévu pour la production durant lequel l’équipement est effectivement disponible pour fonctionner. Elle prend en compte les arrêts planifiés et imprévus.
- Performance : évalue la vitesse à laquelle les produits sont fabriqués par rapport à la vitesse théorique maximale. Cela inclut les ralentissements et les petits arrêts qui n’entraînent pas une cessation complète de la production.
- Qualité : mesure la proportion de produits fabriqués correctement par rapport au total des produits fabriqués, en tenant compte des produits rejetés ou nécessitant une reprise.
Historique de l’OEE et du TRS
L’OEE trouve ses origines dans les années 1960 au Japon, dans le contexte du développement des pratiques de maintenance productive totale (TPM). Ce concept a été développé par Seiichi Nakajima dans le cadre d’un programme visant à maximiser l’efficacité de la production en identifiant et en minimisant les différentes formes de perte dans les processus de fabrication.
À l’origine, l’OEE a été conçu comme un outil de mesure permettant de capturer l’efficacité réelle des équipements de production en tenant compte de toutes les pertes, allant des temps d’arrêt imprévus aux défauts de qualité et aux performances sous-optimales. La genèse de cet indicateur est étroitement liée à l’essor de la philosophie Lean Manufacturing et de la TPM, qui visent toutes deux à éliminer les gaspillages et à améliorer la qualité et l’efficacité.
Le concept de TRS, étant synonyme de l’OEE dans le contexte francophone, a également suivi une trajectoire similaire. Bien qu’il puisse parfois y avoir de légères différences dans l’interprétation ou l’application des deux termes, le TRS partage le même objectif fondamental que l’OEE : fournir une mesure compréhensive de l’efficacité opérationnelle.
Calcul de l’OEE
Le calcul de l’OEE est relativement simple une fois que les données nécessaires sont collectées. La formule de base est :

où chaque terme est un pourcentage. Par exemple, si une machine est disponible 90% du temps (Disponibilité), fonctionne à 75% de sa vitesse maximale (Performance) et produit 95% de pièces de bonne qualité (Qualité), alors l’OEE de cette machine est :

soit 64%. Ce chiffre révèle la véritable efficacité de l’équipement par rapport à son potentiel maximum.
En pratique
Dans un contexte industriel, le calcul de l’OEE permet aux gestionnaires de déterminer où se situent les pertes majeures et d’identifier les domaines spécifiques nécessitant des améliorations. Par exemple, une faible disponibilité peut indiquer un besoin d’améliorer les pratiques de maintenance, tandis qu’une faible performance peut suggérer des problèmes avec les procédures opérationnelles ou les équipements eux-mêmes. De même, une faible qualité peut nécessiter une attention particulière aux matières premières, au processus de fabrication ou aux contrôles de qualité.
En somme, une compréhension profonde de l’OEE et de ses composants, ainsi qu’une application méthodique et réfléchie, peut conduire à des améliorations substantielles dans l’efficacité de la production. En utilisant l’OEE comme un baromètre de performance, les usines peuvent systématiquement détecter les inefficacités, mettre en œuvre des solutions ciblées et, en fin de compte, atteindre des niveaux de productivité optimisés.
Analyse et interprétation des résultats et amélioration continue
L’analyse et l’interprétation des résultats obtenus par le calcul de l’OEE sont cruciales pour toute usine souhaitant optimiser sa productivité. Ces données ne servent pas seulement à quantifier l’efficacité actuelle, mais fournissent également un aperçu précieux sur les domaines spécifiques nécessitant des améliorations. C’est là que la véritable valeur de l’OEE se révèle : en transformant les chiffres en actions concrètes pour accroître l’efficience.
Interprétation des Résultats
Un OEE global peut être décomposé pour révéler des informations sur les différentes sources de perte de productivité. Par exemple, une faible disponibilité peut signaler des problèmes de maintenance ou des pannes fréquentes, tandis qu’une faible performance peut indiquer que les machines fonctionnent en dessous de leur capacité optimale. De même, un faible score de qualité peut révéler des problèmes avec les matières premières, le processus de production ou les standards de qualité.
Il est essentiel d’utiliser ces données pour établir des priorités d’action. Par exemple, si la disponibilité est le principal facteur limitant l’OEE, les efforts devraient se concentrer sur la réduction des temps d’arrêt machine. Cela pourrait inclure l’amélioration des routines de maintenance, la réduction des pannes matérielles ou l’optimisation des changements de production.
Amélioration Continue
La démarche d’amélioration continue repose sur l’identification, l’analyse et la résolution des problèmes mis en lumière par l’OEE. Il est conseillé de suivre une approche structurée telle que la méthodologie TPM (Maintenance Productive Totale) qui vise à augmenter l’efficacité de l’équipement en impliquant tous les employés, de la direction à la production. Cette approche englobe plusieurs initiatives :
- Maintenance autonome : Elle habilite les opérateurs à effectuer des contrôles réguliers et de base, ce qui aide à prévenir les pannes et à améliorer la disponibilité.
- Amélioration focalisée : Des équipes dédiées identifient les causes racines des pertes et mettent en œuvre des solutions pour améliorer l’OEE.
- Maintenance planifiée : Un programme de maintenance régulier et préventif réduit les pannes et les arrêts imprévus.
La méthode SMED (Single-Minute Exchange of Die) peut également être appliquée pour réduire significativement les temps de changement et augmenter ainsi la disponibilité de l’équipement.
Conseils pour l’Amélioration des Composants de l’OEE
- Disponibilité : Réduisez les arrêts machine en améliorant les procédures de maintenance et en formant le personnel à identifier et à résoudre rapidement les problèmes courants.
- Performance : Identifiez et éliminez les goulets d’étranglement, optimisez les réglages des machines et standardisez les processus de travail pour assurer un fonctionnement efficace et régulier.
- Qualité : Renforcez les contrôles de qualité à toutes les étapes de production et utilisez des retours d’information pour corriger les problèmes en amont, réduisant ainsi le nombre de défauts et de retouches.
Application Pratique
Dans la pratique, l’analyse des résultats OEE doit être accompagnée d’un plan d’action clair et suivi régulièrement. Cela peut impliquer la mise en place de tableaux de bord pour suivre les progrès, la formation continue du personnel et l’établissement de cibles de performance réalistes mais ambitieuses.
Pour cela, vous pouvez décider de passer par des outils dédiés qui vous permettront de faciliter la démarche à tous les niveaux de management. C’est ce que propose Shizen, en encourageant tous les utilisateurs dans la démarche globale d’amélioration pour éradiquer davantage de problèmes, et mettre en place les actions de la bonne manière et au bon niveau.
L’amélioration de l’OEE est un processus continu qui nécessite un engagement à long terme. Par exemple, une entreprise peut commencer par se concentrer sur la réduction des temps d’arrêt dus aux pannes, puis progressivement aborder des problèmes de performance et de qualité à mesure que les processus de maintenance et de production s’améliorent.
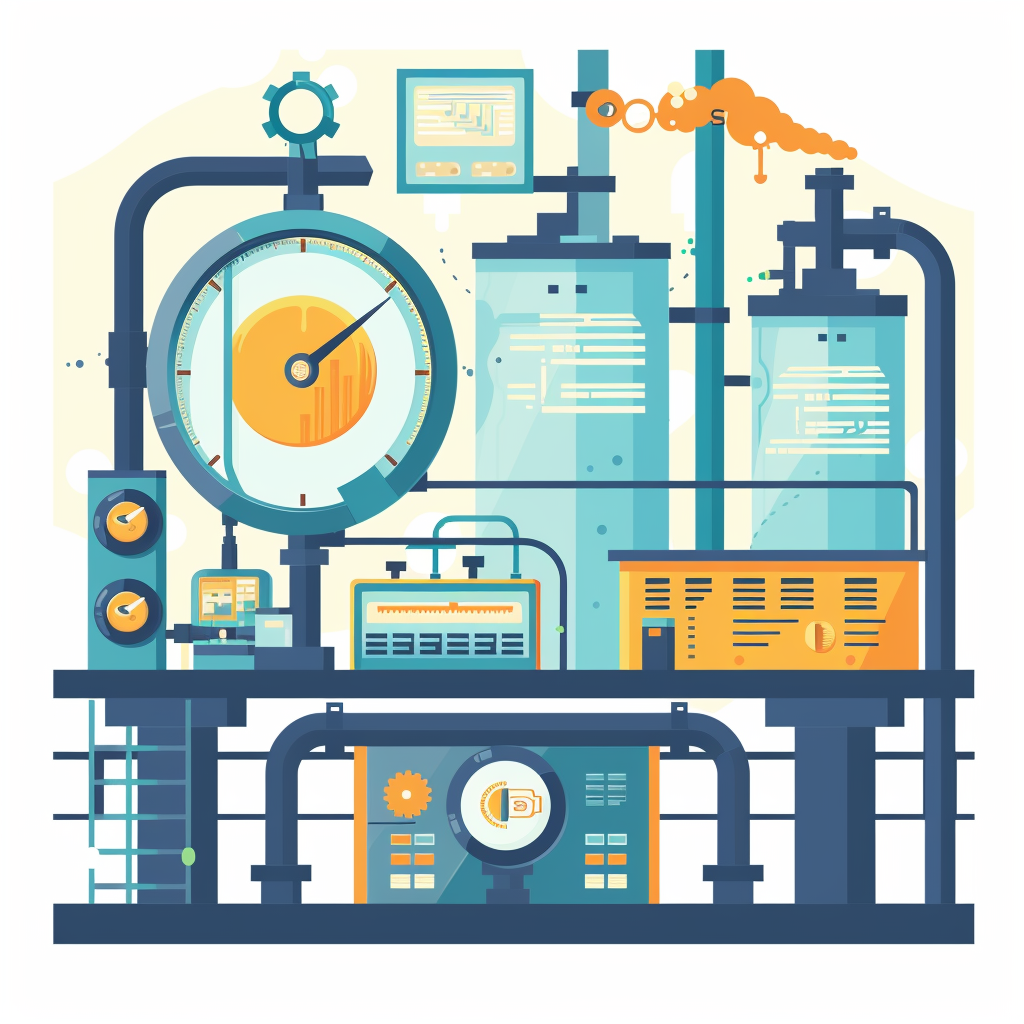
Implémentation de l’OEE dans votre usine, quelques outils
Étapes pour la mise en place de l’OEE
- Engagement de la direction : Tout commence par l’engagement de la direction. Sans soutien à ce niveau, il sera difficile de mobiliser les ressources nécessaires et de prioriser les activités d’amélioration. La direction doit être clairement convaincue de l’importance de l’OEE / TRS comme éléments clés de la stratégie globale de l’entreprise.
- Formation et sensibilisation : Il est crucial que le personnel concerné comprenne ce qu’est l’OEE, pourquoi il est important et comment il peut contribuer à l’amélioration. Des formations régulières et des sessions de sensibilisation aideront à aligner tous les employés sur les objectifs communs, même si celles-ci sont courtes et simples.
- Identification des équipements clés : Commencez par identifier et évaluer les lignes de production ou les machines qui sont cruciales pour votre processus de production. Cela permettra de concentrer vos efforts là où ils auront le plus grand impact, en suivant le principe de Pareto.
- Collecte de données : L’exactitude des données est essentielle pour calculer de manière fiable l’OEE. Assurez-vous que les procédures de collecte de données sont en place et que le personnel est formé pour les exécuter correctement.
- Analyse des données et identification des problèmes : Utilisez les données collectées pour identifier où se situent les pertes et les inefficacités. Analysez les tendances et déterminez les causes profondes des problèmes, notamment grâce à des outils de résolution de problèmes, comme Shizen.
- Mise en œuvre de solutions et suivi des progrès : Une fois les problèmes identifiés, travaillez à la mise en place de solutions pour les résoudre. Suivez les améliorations au fil du temps et ajustez les plans d’action selon les résultats obtenus.
Outils et technologies de suivi de l’OEE et du TRS
Pour faciliter le calcul et le suivi de l’OEE / TRS, de nombreuses entreprises se tournent vers des solutions logicielles et matérielles. Comme nous l’avons dit plus haut, Shizen propose notamment des outils de résolution de problèmes et les suivis de plans d’action associés, le tout en lien avec vos propres KPIs. Shizen met un point d’honneur à suivre des méthodologies Lean bien connues, comme le DMAIC, le 8D, le PDCA, etc. De plus, Shizen se connecte très facilement avec d’autres outils que vous pourriez connaître :
- Logiciels de gestion de la production (MES) : Les systèmes MES (Manufacturing Execution System) peuvent automatiser la collecte et l’analyse des données de production, fournissant des informations en temps réel sur l’OEE. Ces systèmes facilitent le suivi des progrès et la prise de décisions basée sur des données précises.
- Tableaux de bord et visualisation des données : Des outils de visualisation tels que les tableaux de bord interactifs permettent de suivre les performances en temps réel et d’identifier rapidement les domaines nécessitant une attention. Ils rendent les données accessibles et compréhensibles pour tous les niveaux de l’organisation.
- Solutions de maintenance prédictive : L’intégration de technologies de maintenance prédictive peut réduire les temps d’arrêt imprévus et améliorer la disponibilité, un composant clé de l’OEE. Des capteurs et des logiciels d’analyse aident à prévoir les défaillances avant qu’elles ne surviennent.
- Outils d’amélioration continue : Des méthodologies comme la TPM et le SMED peuvent être soutenues par des outils spécifiques, y compris des logiciels de gestion des tâches et de suivi des progrès, pour optimiser les processus de maintenance et réduire les temps de changement.
Importance de la culture d’entreprise
L’adoption de l’OEE ne se limite pas à l’utilisation de nouveaux outils ou à la modification des processus ; elle nécessite un changement culturel au sein de l’entreprise. Encouragez une culture de transparence, où les employés se sentent responsabilisés pour signaler les problèmes et proposer des solutions. Reconnaître et récompenser les contributions à l’amélioration de l’OEE peut renforcer l’engagement des employés et favoriser un environnement de travail collaboratif orienté vers l’amélioration continue.
Conclusion
En résumé, l’OEE et le TRS sont des indicateurs essentiels pour mesurer et améliorer la productivité dans le secteur industriel. Leur mise en œuvre permet d’identifier précisément les sources de perte et de mettre en place des actions ciblées pour améliorer la performance des équipements. La démarche nécessite l’engagement de tous les niveaux de l’entreprise et l’utilisation d’outils adaptés pour le suivi et l’analyse.
L’intégration réussie de l’OEE peut transformer les opérations de production, conduisant à des gains significatifs en termes d’efficacité et de rentabilité. Nous encourageons les usines à adopter ces mesures comme une partie intégrale de leur gestion de la performance pour réaliser leur plein potentiel productif.
Embrasser l’OEE n’est pas seulement un investissement dans des outils de mesure, mais un engagement envers une culture d’amélioration continue et d’excellence opérationnelle. En avançant sur la voie de l’optimisation, votre usine peut non seulement atteindre mais dépasser ses objectifs de productivité.