La TPM, ou Total Productive Maintenance, est une méthode de gestion de la maintenance qui vise à améliorer la performance et la qualité des équipements et des processus industriels. Elle repose sur l’implication de tous les employés, du niveau opérationnel au niveau stratégique, dans la prévention et la résolution des problèmes liés aux machines. Elle s’inscrit dans une démarche d’amélioration continue et d’excellence opérationnelle.
Définition de la TPM
La TPM peut se définir comme une stratégie de maintenance qui cherche à optimiser le taux de rendement synthétique (TRS) des équipements en réduisant les pertes dues aux pannes, aux arrêts, aux changements de série, aux défauts de qualité ou aux accidents. Le TRS est un indicateur qui mesure le rapport entre le temps productif réel et le temps productif théorique d’un équipement. Il se calcule en multipliant le taux de disponibilité, le taux de performance et le taux de qualité.
La TPM vise à atteindre un TRS proche de 100%, ce qui signifie que les équipements fonctionnent sans interruption, à leur pleine capacité et sans générer de rebuts ou de retouches. Pour cela, la TPM s’appuie sur huit piliers qui définissent les axes d’amélioration à mettre en œuvre.
Histoire et évolution de la TPM
La TPM est née au Japon dans les années 1970, sous l’impulsion du Japan Institute of Plant Maintenance (JIPM). Elle s’inspire des principes du lean manufacturing, une méthode d’optimisation des flux de production développée par Toyota. Elle intègre également des concepts issus du total quality management (TQM), une approche centrée sur la satisfaction du client par la maîtrise de la qualité.
La TPM a connu plusieurs évolutions au fil du temps, en fonction des besoins et des enjeux des entreprises. Elle est passée d’une approche centrée sur la maintenance préventive à une approche intégrée qui englobe la conception, l’exploitation, la formation et l’innovation. Elle a également élargi son champ d’application au-delà du secteur manufacturier, en s’adaptant aux secteurs tels que la distribution, les services ou l’informatique.
Les principes fondamentaux de la TPM
Les huit piliers de la TPM
La TPM repose sur huit piliers qui définissent les domaines d’action pour améliorer la performance des équipements. Ces piliers sont les suivants :
- L’amélioration ciblée : il s’agit d’identifier et d’éliminer les causes racines des pertes chroniques ou sporadiques qui affectent le TRS. Pour cela, on utilise des méthodes telles que le PDCA (plan-do-check-act) ou le DMAIC (define-measure-analyze-improve-control).
- La maintenance autonome : il s’agit d’impliquer les opérateurs dans les tâches quotidiennes de nettoyage, de contrôle, de réglage et de lubrification des équipements. Cela permet de prévenir les pannes, d’améliorer les conditions de travail et de renforcer les compétences du personnel.
- La maintenance planifiée : il s’agit d’optimiser la planification et l’exécution des interventions de maintenance préventive, corrective et prédictive. Cela permet de réduire les coûts, les délais et les risques liés à la maintenance.
- La formation et l’éducation : il s’agit de développer les connaissances et les aptitudes du personnel en matière de maintenance, de qualité, de sécurité et d’amélioration continue. Cela permet d’accroître la motivation, la responsabilisation et la polyvalence des employés.
- L’amélioration du niveau initial : il s’agit d’intégrer les exigences de la TPM dès la conception ou l’achat des nouveaux équipements. Cela permet de garantir leur fiabilité, leur facilité d’utilisation et leur adaptabilité aux besoins du client.
- La maintenance de la qualité : il s’agit de prévenir et de réduire les défauts de qualité en améliorant les processus, les méthodes et les outils de contrôle. Cela permet de satisfaire les attentes du client et de réduire les coûts de non-qualité.
- La maintenance du lieu de travail : il s’agit d’améliorer l’organisation, la propreté et la sécurité du lieu de travail en appliquant les principes du 5S (seiri, seiton, seiso, seiketsu, shitsuke). Cela permet de créer un environnement propice à la performance et au bien-être des employés.
- La sécurité, l’hygiène et l’environnement : il s’agit de prévenir et de réduire les accidents, les maladies professionnelles et les impacts environnementaux liés aux activités de production. Cela permet de protéger la santé des employés, des clients et de la société.
L’importance de l’implication de tous les employés
La TPM est une méthode participative qui requiert l’implication de tous les employés, quel que soit leur niveau hiérarchique ou fonctionnel. En effet, la TPM repose sur l’idée que chacun est responsable de la performance et de la qualité des équipements qu’il utilise ou qu’il supervise. Ainsi, la TPM encourage la communication, la coopération et le partage des bonnes pratiques entre les différents acteurs de l’organisation.
L’implication des employés se traduit par plusieurs actions concrètes, telles que :
- La formation continue sur les principes, les méthodes et les outils de la TPM.
- La participation aux groupes de travail ou aux cercles de qualité pour identifier et résoudre les problèmes liés aux équipements.
- L’application des standards et des procédures définis pour assurer la maintenance autonome des équipements.
- L’enregistrement et le suivi des indicateurs de performance et de qualité des équipements.
- La proposition et la mise en œuvre d’idées d’amélioration continue.
La stratégie de maintenance en continu
La TPM est une méthode qui vise à optimiser la stratégie de maintenance en continu des équipements. La maintenance en continu consiste à adapter le type et la fréquence des interventions de maintenance en fonction des besoins réels des équipements. Elle repose sur une analyse approfondie des données historiques, des conditions opérationnelles et des objectifs stratégiques. Elle permet ainsi d’éviter le sous-maintenance ou le sur-maintenance, qui peuvent entraîner des pertes ou des gaspillages.
La maintenance en continu se décline en trois types principaux :
- La maintenance préventive : il s’agit d’effectuer des interventions planifiées à intervalles réguliers ou selon un nombre déterminé d’utilisations. L’objectif est d’éviter l’apparition d’une défaillance ou d’une usure prématurée des équipements.
- La maintenance corrective : il s’agit d’effectuer des interventions non planifiées suite à une défaillance ou à une anomalie constatée sur les équipements. L’objectif est de rétablir le fonctionnement normal des équipements dans les meilleurs délais.
- La maintenance prédictive : il s’agit d’effectuer des interventions basées sur l’analyse en temps réel des paramètres de fonctionnement des équipements. L’objectif est de détecter les signes précurseurs d’une défaillance ou d’une dégradation des performances et d’intervenir avant qu’elles ne se produisent.
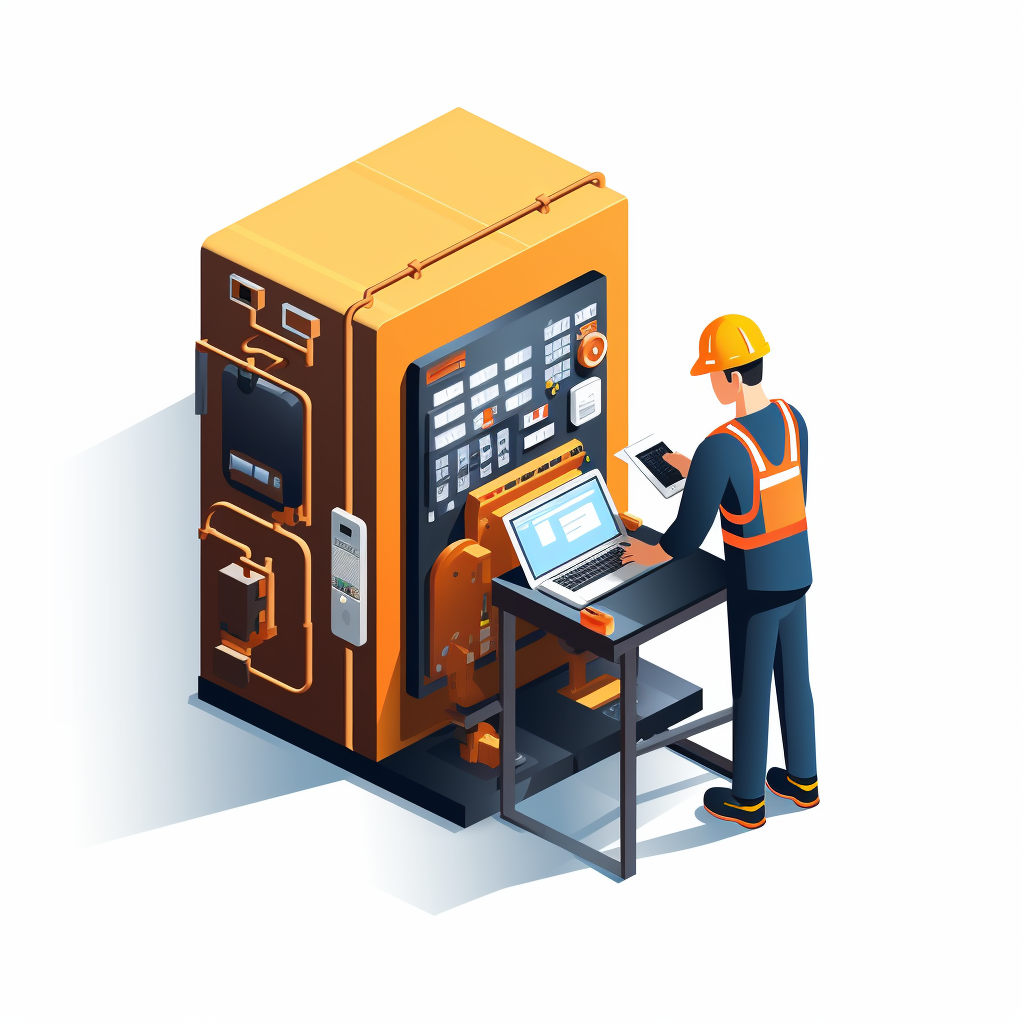
Comment mettre en œuvre la TPM dans votre organisation
Comprendre le paysage actuel de la maintenance
Avant de lancer un projet de TPM, il est essentiel de réaliser un diagnostic de la situation actuelle de la maintenance dans votre organisation. Cela vous permettra d’identifier les forces, les faiblesses, les opportunités et les menaces liées à votre système de maintenance. Vous pourrez ainsi définir les priorités, les enjeux et les axes d’amélioration pour votre projet de TPM.
Pour réaliser ce diagnostic, vous pouvez utiliser des outils tels que :
- Le questionnaire TPM : il s’agit d’un outil d’auto-évaluation qui permet de mesurer le niveau de maturité de votre organisation en matière de TPM. Il se compose d’une trentaine de questions portant sur les huit piliers de la TPM. Il vous permettra d’obtenir un score global et un score par pilier, ainsi que des recommandations pour progresser.
- L’audit TPM : il s’agit d’un outil d’évaluation externe qui permet de vérifier la conformité et l’efficacité de votre système de maintenance par rapport aux exigences de la TPM. Il se base sur une grille d’évaluation qui couvre les aspects stratégiques, organisationnels, techniques et humains de la TPM. Il vous permettra d’obtenir un rapport détaillé avec des points forts, des points faibles et des pistes d’amélioration.
- L’analyse des pertes : il s’agit d’un outil d’analyse qui permet d’identifier et de quantifier les pertes qui affectent le TRS de vos équipements. Il se base sur une classification des pertes en six catégories : les pannes, les arrêts, les changements de série, les démarrages, les défauts et les rebuts. Il vous permettra d’établir un diagramme de Pareto qui met en évidence les principales sources de pertes et les opportunités d’amélioration.
Définir les objectifs et les KPIs
Après avoir réalisé le diagnostic de la situation actuelle, il est important de définir les objectifs et les indicateurs clés de performance (KPIs) pour votre projet de TPM. Les objectifs doivent être SMART, c’est-à-dire spécifiques, mesurables, atteignables, réalistes et temporels. Ils doivent être alignés avec la vision, la mission et la stratégie globale de votre organisation. Ils doivent également être partagés et acceptés par tous les acteurs impliqués dans le projet.
Les KPIs sont des mesures quantitatives ou qualitatives qui permettent d’évaluer l’avancement et le succès du projet. Ils doivent être pertinents, fiables, simples et faciles à communiquer. Ils doivent être définis pour chaque pilier de la TPM et pour chaque niveau de l’organisation. Ils doivent être suivis régulièrement et comparés aux objectifs fixés.
Quelques exemples d’objectifs et de KPIs pour un projet de TPM sont :Les étapes de la mise en place de la TPM La mise en place de la TPM dans votre organisation nécessite une démarche structurée et progressive qui se déroule en plusieurs étapes. Ces étapes sont les suivantes :
- Augmenter le TRS des équipements critiques de 20% en un an.
- Réduire le nombre d’accidents du travail liés aux équipements de 50% en six mois.
- Améliorer la satisfaction client en termes de qualité et de délai de livraison de 10% en trois mois.
- Augmenter le taux de participation aux activités d’amélioration continue de 30% en un an.
Les étapes de la mise en place de la TPM
- L’annonce du projet : il s’agit de communiquer sur le lancement du projet, ses objectifs, ses bénéfices, ses modalités et ses acteurs. Il faut impliquer la direction générale, les managers et les employés dans cette communication. Il faut également créer une équipe projet qui sera chargée de piloter et de coordonner le projet.
- La formation initiale : il s’agit de former l’équipe projet et les employés aux principes, aux méthodes et aux outils de la TPM. Il faut adapter le contenu et la durée de la formation en fonction du niveau de connaissance et du rôle de chaque participant. Il faut également évaluer l’efficacité de la formation et s’assurer de la compréhension et de l’adhésion des participants.
- La sélection des équipements pilotes : il s’agit de choisir les équipements sur lesquels on va appliquer la TPM en priorité. Il faut sélectionner des équipements qui présentent un fort potentiel d’amélioration, qui sont stratégiques pour la production, qui sont représentatifs des différents types d’équipements et qui sont accessibles pour les interventions.
- L’application des piliers de la TPM : il s’agit de mettre en œuvre les actions d’amélioration définies pour chaque pilier de la TPM sur les équipements pilotes. Il faut respecter le plan d’action établi, impliquer les employés concernés, documenter les résultats obtenus et diffuser les bonnes pratiques.
- L’évaluation et l’amélioration : il s’agit de mesurer l’impact du projet sur les KPIs définis, d’analyser les écarts par rapport aux objectifs, d’identifier les points forts et les points faibles du projet, de définir des actions correctives ou préventives et de mettre en place un plan d’amélioration continue.
- L’extension du projet : il s’agit de généraliser le projet à l’ensemble des équipements et des processus de l’organisation, en tenant compte des spécificités et des besoins de chaque zone ou département. Il faut également pérenniser le projet en intégrant la TPM dans la culture et le système de management de l’organisation.
Les avantages et défis de la TPM
Les bénéfices directs de la TPM
La TPM apporte de nombreux bénéfices directs pour votre organisation, tels que :
- L’amélioration de la performance opérationnelle : la TPM permet d’augmenter le TRS des équipements, ce qui se traduit par une réduction des coûts de production, une augmentation de la productivité, une amélioration de la qualité, une diminution des délais et une optimisation des capacités.
- L’amélioration de la performance financière : la TPM permet de réduire les coûts liés à la maintenance, tels que les coûts de main-d’œuvre, les coûts des pièces détachées, les coûts d’immobilisation ou les coûts indirects. Elle permet également d’accroître le chiffre d’affaires en augmentant la satisfaction et la fidélisation des clients.
- L’amélioration de la performance sociale : la TPM permet d’améliorer les conditions de travail et la sécurité des employés en réduisant les risques d’accidents, en améliorant l’ergonomie et l’environnement des postes de travail, en renforçant les compétences et l’autonomie des employés, en favorisant le travail en équipe et en reconnaissant les efforts et les résultats.
- L’amélioration de la performance environnementale : la TPM permet de réduire l’impact environnemental des activités de production en diminuant la consommation d’énergie, en réduisant les émissions polluantes, en limitant les déchets ou en favorisant le recyclage.
Les défis liés à la mise en œuvre de la TPM
La TPM présente également des défis liés à sa mise en œuvre, tels que :
- Le changement culturel : la TPM implique un changement profond dans la façon de penser et d’agir des employés. Elle demande une forte implication et un engagement de la direction générale, qui doit soutenir et accompagner le projet. Elle nécessite une sensibilisation et une formation de tous les employés, qui doivent adopter une attitude proactive et collaborative dans la maintenance des équipements ; ainsi qu’une communication et une reconnaissance régulières des résultats et des efforts accomplis.
- L’adaptation au contexte : la TPM implique une méthode qui n’est pas figée, mais qui doit être adaptée au contexte spécifique de chaque organisation. Elle nécessite une analyse approfondie des besoins, des attentes, des contraintes et des opportunités de chaque secteur d’activité, de chaque zone géographique, de chaque type d’équipement et de chaque processus.
Comment faire face aux défis courants de la TPM
Assurer la participation et l’engagement de tous les employés
L’un des principaux défis de la TPM est d’assurer la participation et l’engagement de tous les employés, du niveau opérationnel au niveau stratégique. En effet, la TPM repose sur l’idée que chacun est responsable de la performance et de la qualité des équipements qu’il utilise ou qu’il supervise. Ainsi, la TPM nécessite une communication, une coopération et un partage des bonnes pratiques entre les différents acteurs de l’organisation.
Pour relever ce défi, il est important de mettre en place les actions suivantes :
- Communiquer sur le projet : Informer régulièrement les employés sur le projet, ses objectifs, ses bénéfices, ses modalités et ses résultats. Il faut utiliser des canaux adaptés à chaque cible, tels que des réunions, des affiches, des newsletters, des intranets ou des tableaux de bord.
- Former les employés : Former les employés aux principes, aux méthodes et aux outils de la TPM. Il faut adapter le contenu et la durée de la formation en fonction du niveau de connaissance et du rôle de chaque participant.
- Impliquer les employés : Impliquer les employés dans les activités d’amélioration continue liées à la TPM. Il faut leur donner des responsabilités, des moyens et des opportunités pour participer aux groupes de travail ou aux cercles de qualité pour identifier et résoudre les problèmes liés aux équipements. Il faut également leur permettre d’appliquer les standards et les procédures définis pour assurer la maintenance autonome des équipements. Il faut enfin leur encourager à proposer et à mettre en œuvre des idées d’amélioration continue.
- Reconnaître les employés : il s’agit de reconnaître les efforts et les résultats des employés qui participent au projet. Il faut leur donner du feedback positif, les féliciter publiquement, leur attribuer des récompenses symboliques ou matérielles, ou leur offrir des opportunités d’évolution professionnelle.
Maintenir une mise en œuvre efficace sur le long terme
L’autre défi majeur de la TPM est de maintenir une mise en œuvre efficace sur le long terme. En effet, la TPM n’est pas un projet ponctuel, mais une démarche permanente qui vise à améliorer continuellement la performance et la qualité des équipements. Ainsi, la TPM nécessite un suivi et un contrôle rigoureux des activités, des indicateurs, des risques et des opportunités du projet :
- Suivre et contrôler le projet : il s’agit de mesurer et de comparer régulièrement les indicateurs de performance et de qualité des équipements avec les objectifs fixés. Il faut également identifier et analyser les écarts, les risques et les opportunités qui peuvent survenir au cours du projet. Il faut enfin définir et mettre en œuvre des actions correctives ou préventives pour assurer l’atteinte des objectifs.
- Adapter et innover le projet : il s’agit d’adapter le projet aux changements internes ou externes qui peuvent affecter les équipements ou les processus. Il faut également innover en proposant de nouvelles idées ou de nouvelles solutions pour améliorer la performance et la qualité des équipements. Il faut enfin diffuser et capitaliser les bonnes pratiques au sein de l’organisation.
Conclusion: la TPM en tant que stratégie d’excellence opérationnelle
La TPM est une méthode qui a connu plusieurs évolutions au fil du temps, en fonction des besoins et des enjeux des entreprises. Elle est passée d’une approche centrée sur la maintenance préventive à une approche intégrée qui englobe la conception, l’exploitation, la formation et l’innovation. Elle a également élargi son champ d’application au-delà du secteur manufacturier, en s’adaptant aux secteurs tels que la distribution, les services ou l’informatique.
La TPM est une méthode qui continuera à évoluer dans le futur, en fonction des tendances et des opportunités du marché. Parmi ces tendances, on peut citer :
- L’industrie 4.0 : il s’agit du développement des technologies numériques dans l’industrie, telles que l’internet des objets (IoT), le big data, le cloud computing, l’intelligence artificielle (IA) ou la réalité augmentée (RA). Ces technologies permettent de collecter, de traiter, d’analyser et de partager des données en temps réel sur les équipements et les processus. Elles offrent ainsi de nouvelles possibilités pour optimiser la performance, la qualité, la sécurité et l’environnement des systèmes productifs.
- L’agilité organisationnelle : capacité à s’adapter rapidement et efficacement aux changements internes ou externes qui affectent l’organisation. Elle implique de développer une culture de l’apprentissage, de la collaboration, de l’innovation et de l’amélioration continue. Elle offre ainsi de nouvelles opportunités pour renforcer la compétitivité, la flexibilité et la résilience des systèmes productifs.
Enfin, la TPM reste un levier essentiel pour atteindre l’excellence opérationnelle et créer de la valeur ajoutée pour l’organisation.