Le principe de Pareto intervient dans un monde industriel en constante évolution, où l’efficacité et l’optimisation des processus sont devenues des piliers fondamentaux pour assurer la compétitivité et la pérennité des entreprises. Également connu sous le nom de règle 80/20, le principe de Pareto est une théorie qui a révolutionné la manière dont les organisations identifient et abordent leurs problématiques principales. Cet article vise à décomposer le principe de Pareto, en soulignant son importance et son applicabilité dans le secteur industriel. Nous explorerons comment l’adoption de ce principe peut mener à des améliorations significatives en termes de gestion de la qualité, de la production et des ressources, en se concentrant sur les aspects qui apportent le plus de valeur.
I. Fondements du Principe de Pareto
Origine du diagramme de Pareto et développement historique par Vilfredo Pareto.
Le principe de Pareto, formulé pour la première fois par l’économiste italien Vilfredo Pareto à la fin du XIXe siècle, repose sur une observation initiale selon laquelle environ 80 % des terres en Italie étaient possédées par 20 % de la population. Cette découverte, bien que simple en apparence, a mis en lumière une répartition inégale mais prévisible des ressources et des efforts qui s’applique à une multitude de domaines, pas seulement économiques mais aussi sociaux, scientifiques et industriels.
Explication du principe 80/20 et son interprétation dans différents contextes.
Dans l’industrie, le principe de Pareto est devenu un outil précieux pour analyser et améliorer les processus de production. Il postule que 80 % des problèmes ou des résultats sont souvent le produit de 20 % des causes. Cette relation n’est pas fixe ni universellement applicable dans les mêmes proportions, mais elle offre un cadre pour identifier et prioriser les zones d’action qui promettent le plus grand impact. Par exemple, dans une usine, cela pourrait signifier que 20 % des défauts de produits sont à l’origine de 80 % des réclamations des clients, ou que 20 % des lignes de produits génèrent 80 % du chiffre d’affaires.
L’application de cette règle permet aux gestionnaires et aux équipes de se concentrer sur les « 20 % critiques » qui nécessitent le plus d’attention, optimisant ainsi les ressources et les efforts pour corriger les plus grands générateurs de coûts ou de problèmes. Cette approche ciblée ne se limite pas à la résolution de problèmes; elle s’étend également à la maximisation de l’efficacité et à l’allocation stratégique des ressources dans divers aspects de la production et de la gestion de la qualité.
Signification et implications du principe de Pareto pour les entreprises.
En déployant le principe de Pareto, les industries peuvent non seulement identifier les principaux contributeurs aux problèmes et aux succès mais aussi structurer leurs initiatives d’amélioration continue de manière plus stratégique. La prochaine section développera comment ce principe est appliqué concrètement dans les processus de fabrication et de production, en fournissant des cadres et des méthodologies pour exploiter pleinement le potentiel du principe de Pareto dans l’amélioration des performances industrielles.
II. Le Diagramme de Pareto et Son Application en Industrie
Composition et construction du diagramme de Pareto.
Le diagramme de Pareto, un outil visuel et analytique, joue un rôle clé dans l’identification et la hiérarchisation des problèmes au sein des entreprises industrielles. Sa construction commence par la collecte de données sur les incidents, les défauts ou les retards, classés par catégorie. Chaque catégorie est ensuite évaluée en fonction de sa fréquence ou de son impact, permettant de tracer un histogramme où les catégories sont disposées en ordre décroissant.
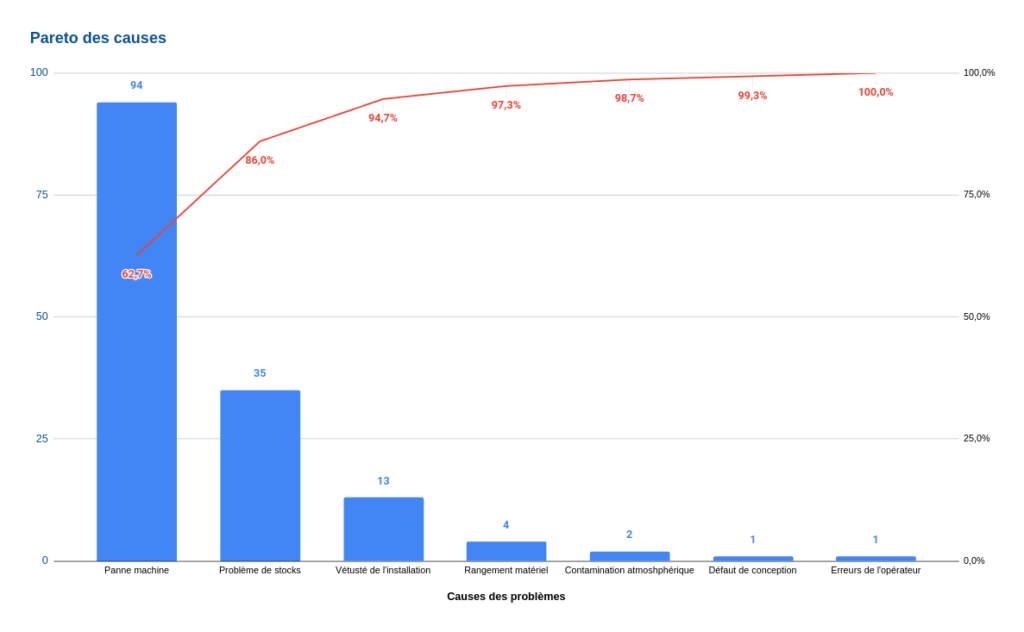
Méthodologie d’application et étapes pour réaliser un diagramme de Pareto efficace
La méthodologie pour élaborer un diagramme de Pareto efficace implique plusieurs étapes clés. Initialement, il est nécessaire de définir clairement le problème à analyser. Par la suite, les données recueillies doivent être triées et classées pour identifier les principales causes des problèmes. Lors de la création du diagramme, les problèmes sont représentés par des barres, et une ligne cumulative est ajoutée pour illustrer le pourcentage total des effets ou des coûts attribuables à chaque cause. Cela aide à visualiser comment les petites portions (les 20 %) contribuent majoritairement (les 80 %) aux résultats ou aux problèmes.
Analyse et interprétation des résultats obtenus à partir du diagramme
Une fois le diagramme de Pareto établi, l’analyse et l’interprétation des données deviennent cruciales pour déterminer les actions significatives et ciblées. Cette phase comprend plusieurs étapes clés, essentielles pour transformer les observations en décisions stratégiques et tactiques efficaces.
- Hiérarchisation des Problèmes : La première étape consiste à examiner les barres du diagramme, qui représentent les différentes causes des problèmes, par leur hauteur, reflétant leur fréquence ou leur gravité. Les problèmes sont classés de manière décroissante, permettant ainsi de visualiser rapidement ceux qui ont le plus grand impact sur les opérations.
- Identification des « 20 % » Clés : En se concentrant sur la partie gauche du diagramme, identifiez les premières causes (généralement les deux ou trois premières barres) qui contribuent à une majorité des problèmes (souvent jusqu’à 80 %). Ces « 20 % » représentent les cibles prioritaires pour les actions correctives.
- Analyse de la Courbe Cumulative : La ligne cumulée, qui croise généralement les barres, aide à identifier le point où les contributions des causes individuelles atteignent un seuil significatif (souvent 80 %). Ce point d’intersection indique jusqu’où l’entreprise doit se concentrer pour réaliser des améliorations significatives.
- Évaluation de la Distribution des Problèmes : Une distribution très inclinée (où quelques problèmes dominent clairement) confirme la validité de l’application du principe de Pareto. En revanche, une distribution plus uniforme peut indiquer que des forces différentes ou plus diffuses impactent les opérations, nécessitant une stratégie différente.
- Détermination des Actions Correctives : Basées sur l’analyse, les actions correctives doivent être priorisées en fonction de leur potentiel d’impact. Cela signifie se concentrer d’abord sur les problèmes les plus critiques. Chaque action devrait être définie avec des objectifs clairs, des responsabilités et des délais pour sa mise en œuvre.
- Suivi et Réévaluation : Après la mise en œuvre des actions correctives, il est crucial de suivre les progrès et de réévaluer périodiquement la situation. Le diagramme de Pareto doit être régulièrement mis à jour pour refléter les changements et pour vérifier l’efficacité des mesures prises. Si les problèmes initiaux ont été résolus ou significativement réduits, de nouveaux problèmes peuvent émerger comme les nouveaux « 20 % » à cibler.
En résumé, l’analyse et l’interprétation des résultats du diagramme de Pareto doivent mener à une compréhension profonde des problèmes les plus importants auxquels l’entreprise est confrontée. Nous y reviendrons dans la partie 4.
III. Cas Pratiques et Domaines d’Application
Utilisation du diagramme de Pareto dans le management de la qualité et l’amélioration continue
Le diagramme de Pareto trouve son application dans divers domaines au sein de l’industrie, notamment dans le management de la qualité et l’amélioration continue. En identifiant les défauts de production ou les erreurs opérationnelles qui sont les plus fréquents ou les plus coûteux, les entreprises peuvent implémenter des stratégies ciblées pour améliorer la qualité de leurs produits ou services. Le Pareto est un incontournable d’une démarche Lean et de la boite à outils du manager Lean.
Exemples d’application
Dans la gestion des ressources par exemple, le diagramme de Pareto s’avère être un outil précieux pour optimiser l’allocation des ressources matérielles, humaines et financières. Un exemple concret de son application peut être observé dans la gestion de l’inventaire d’une usine. Typiquement, toutes les pièces ou matières premières ne sont pas d’égale importance : certaines sont utilisées plus fréquemment ou coûtent plus cher.
En appliquant le diagramme de Pareto, l’entreprise peut identifier les 20 % des articles qui représentent 80 % de la valeur totale de l’inventaire ou de la consommation. Cette analyse permet ensuite de mettre en place une stratégie de gestion différenciée, concentrant les efforts de suivi, de réapprovisionnement et de négociation des prix sur ces articles critiques, tout en réduisant le niveau de stock et les coûts associés aux articles moins importants.
Autre exemple avec la gestion des risques : le diagramme de Pareto aide les entreprises à identifier et à prioriser les risques en fonction de leur fréquence d’apparition et/ou de leur impact potentiel sur l’entreprise. Par exemple, dans une usine de fabrication, les gestionnaires peuvent utiliser le diagramme pour analyser les incidents de sécurité survenus au cours d’une période donnée. Ils pourraient découvrir que 20 % des types d’incidents sont responsables de 80 % des blessures ou des arrêts de production.
Cette connaissance permet alors de concentrer les ressources et les efforts de prévention sur ces incidents spécifiques, réduisant de manière significative le taux global d’accidents et améliorant la sécurité et l’efficacité opérationnelle. En outre, cette approche ciblée aide à allouer de manière optimale le budget de sécurité, en investissant dans les équipements, les formations ou les mesures de prévention qui auront l’impact le plus significatif.
IV. Analyse et Résolution de Problèmes avec le Diagramme de Pareto
L’utilisation efficace du diagramme de Pareto dans l’analyse et la résolution de problèmes repose sur une démarche structurée et une réflexion critique. La première étape consiste à identifier les problèmes les plus significatifs en utilisant le diagramme comme outil d’analyse visuelle. Cette identification permet de cibler les efforts là où ils sont le plus nécessaires, en se concentrant sur les causes profondes qui ont le plus grand impact sur les résultats ou les performances.
Une bonne approche pour identifier les vrais problèmes consiste à passer par le terrain. Les tournées terrain, ou gemba walks sont un outil efficace pour cela.
Démarche DMAIC
Pour résoudre les problèmes, le Pareto se marie parfaitement avec la méthode DMAIC :
- Définir : Identifiez clairement le problème ou l’objectif de performance à améliorer. Utilisez le diagramme de Pareto pour cibler les problèmes les plus critiques qui nécessitent une intervention.
- Mesurer : Collectez des données précises et fiables pour quantifier le problème. Ceci peut inclure le nombre de défauts, la fréquence des retards, etc.
- Analyser : Examinez les causes profondes des problèmes. À ce stade, le 5 pourquoi et le diagramme d’Ishikawa peuvent être utilisés pour explorer toutes les causes possibles des problèmes identifiés. Et la Pareto aide à prioriser en déterminant les causes les plus impactantes.
- Innover (Améliorer) : Développez et mettez en œuvre des solutions pour aborder les causes profondes identifiées. Priorisez les interventions basées sur l’impact potentiel identifié par l’analyse de Pareto.
- Contrôler : Mettez en place des systèmes pour surveiller les améliorations et garantir que les changements sont durables. Répétez l’analyse de Pareto pour confirmer que les problèmes prioritaires ont été résolus.
Une fois les problèmes prioritaires identifiés, la prise de décision éclairée devient possible. Les décideurs peuvent allouer les ressources de manière stratégique, concentrant le temps, le personnel et le budget sur les domaines qui offriront le meilleur retour sur investissement. Cette allocation ciblée des ressources contribue non seulement à une résolution efficace des problèmes mais favorise également une amélioration continue des processus.
Bien entendu, le DMAIC n’est pas l’unique méthode et le Pareto a tout à fait sa place dans un PDCA ou dans un A3 de résolution de problèmes. Il n’est d’ailleurs pas nécessaire d’appliquer une méthode de résolution de problème à la lettre pour utiliser le Pareto.
Conseils pour une mise en œuvre réussie
Pour garantir une mise en œuvre réussie du diagramme de Pareto dans les processus d’amélioration, il est essentiel d’adopter une approche collaborative, impliquant toutes les parties prenantes concernées. La communication claire des constatations et des plans d’action, la formation continue et l’encouragement de la rétroaction peuvent renforcer l’engagement de l’équipe et favoriser un environnement propice à l’amélioration continue.
V. Dépasser les Limites du Principe de Pareto
Malgré sa grande utilité, le principe de Pareto n’est pas sans limites. Il est important de reconnaître que tous les problèmes ne peuvent pas être résolus en se concentrant uniquement sur les « 20 % » de causes principales. Dans certains cas, les « 80 % » restants peuvent contenir des problèmes latents ou des opportunités d’amélioration qui méritent votre attention.
Pour dépasser ces limites, il est conseillé de combiner le principe de Pareto avec d’autres outils et méthodes d’analyse, tels que l’analyse des causes racines, le brainstorming ou les techniques de Six Sigma. L’intégration de ces approches complémentaires peut fournir une compréhension plus nuancée et complète des défis auxquels l’entreprise est confrontée.
En outre, il est crucial de maintenir une approche flexible et adaptable, prête à réévaluer et à ajuster les priorités en fonction de l’évolution du contexte industriel et des résultats des actions d’amélioration. Encourager une culture d’innovation et d’apprentissage continu peut aider les entreprises à rester compétitives et à maximiser l’efficacité du principe de Pareto.
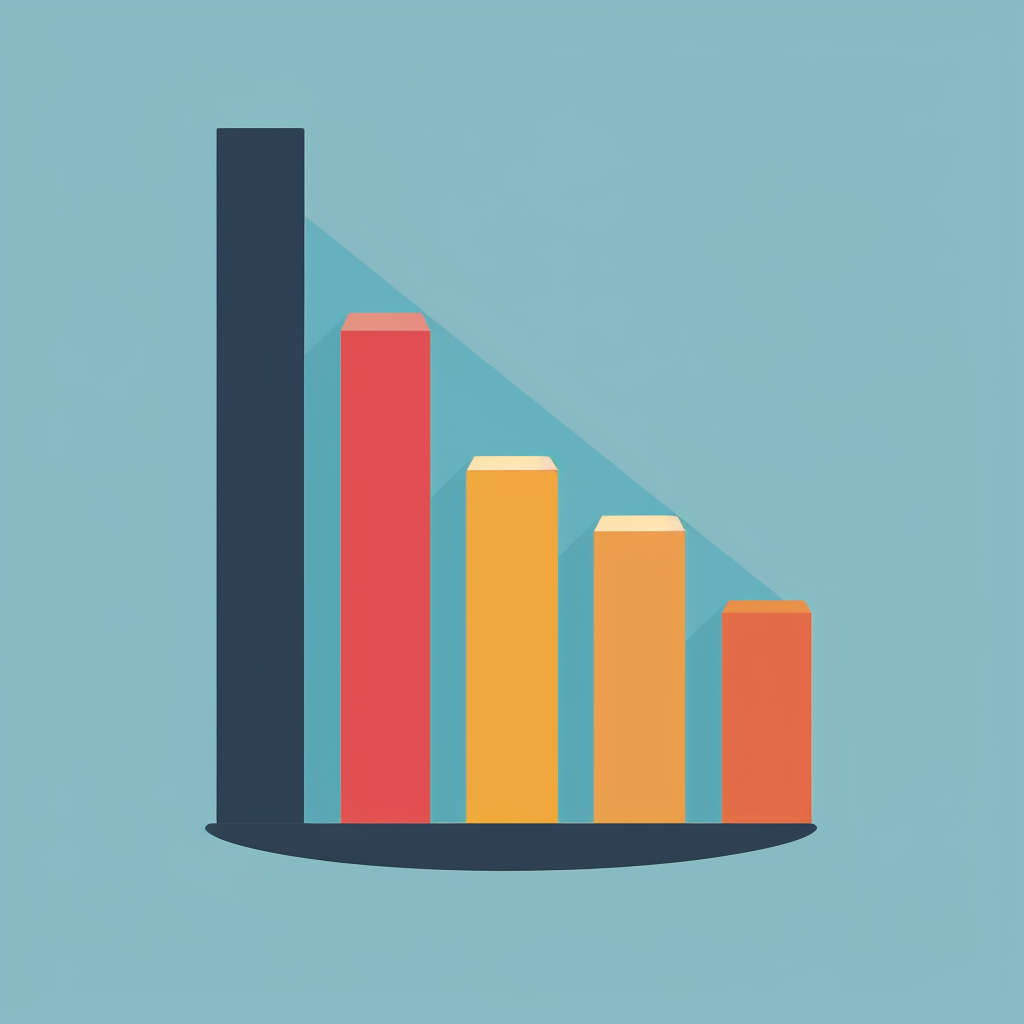
Conclusion
Le principe de Pareto est un outil puissant pour l’optimisation industrielle, offrant une méthode pour identifier et concentrer les efforts sur les aspects les plus critiques des opérations. Son application peut conduire à des améliorations significatives en termes de qualité, d’efficacité et de rentabilité. Cependant, pour réaliser pleinement son potentiel, il doit être appliqué judicieusement, en combinaison avec d’autres outils et dans le cadre d’une stratégie d’amélioration continue bien planifiée.
Nous encourageons les professionnels et les décideurs de l’industrie à adopter le principe de Pareto, non comme une solution universelle, mais comme un composant clé d’une approche globale visant à l’excellence opérationnelle. En poursuivant l’apprentissage et l’adaptation, les entreprises peuvent non seulement résoudre les problèmes actuels mais aussi anticiper et prévenir les défis futurs.