Dans le contexte de la production industrielle, la standardisation joue un rôle crucial dans l’optimisation des processus. Elle consiste à établir des normes et des procédures uniformes pour garantir une qualité constante et améliorer l’efficacité opérationnelle. En standardisant les méthodes de travail, les entreprises peuvent minimiser les variations, réduire les erreurs et assurer une production régulière et de haute qualité.
Pour les usines françaises, l’adoption de pratiques de standardisation est essentielle pour rester compétitives sur un marché globalisé. La standardisation permet non seulement d’améliorer la qualité des produits et de réduire les coûts de production, mais elle contribue également à renforcer la sécurité au travail et à augmenter la productivité globale. En mettant en œuvre des standards rigoureux, les usines peuvent répondre plus efficacement aux exigences des clients et aux régulations industrielles, tout en facilitant l’intégration de nouvelles technologies et l’amélioration continue des processus.
Cet article explore en profondeur la définition et les avantages de la standardisation dans la production industrielle, en mettant en lumière les outils et méthodes clés, les étapes de mise en œuvre et l’impact de ces pratiques sur la performance globale des usines.
Comprendre la Standardisation
Définition et Objectifs de la Standardisation
La standardisation dans la production industrielle consiste à établir des procédures et des normes uniformes pour assurer la cohérence et la qualité des produits et des processus. Cette approche vise à réduire les variations et à garantir que chaque produit répond aux mêmes critères de qualité, quelles que soient les conditions de production. Les principaux objectifs de la standardisation incluent :
- Amélioration de la Qualité : En appliquant des standards rigoureux, les entreprises peuvent s’assurer que chaque produit respecte les mêmes normes de qualité, ce qui réduit les défauts et les rebuts.
- Efficacité Opérationnelle : La standardisation permet de simplifier les processus, de réduire les temps de cycle et d’optimiser l’utilisation des ressources.
- Réduction des Coûts : En minimisant les variations et les erreurs, la standardisation contribue à réduire les coûts de production et à améliorer la rentabilité.
- Sécurité et Conformité : En établissant des procédures standardisées, les entreprises peuvent mieux se conformer aux réglementations et assurer la sécurité des employés.
Historique et Évolution de la Standardisation dans l’Industrie
La standardisation a ses racines dans les premières pratiques industrielles, où l’objectif principal était de garantir la cohérence des produits fabriqués en grande série. Au début du XXe siècle, des pionniers comme Henry Ford ont introduit des concepts de production standardisée dans leurs usines, révolutionnant ainsi l’industrie automobile et établissant les bases de la production de masse.
Avec l’émergence du lean manufacturing dans les années 1980, la standardisation a pris une nouvelle dimension. Inspirée par le système de production de Toyota, cette approche met l’accent sur l’élimination des gaspillages (muda) et l’amélioration continue (kaizen). La standardisation est devenue un élément central de cette philosophie, permettant de stabiliser les processus avant de les améliorer de manière continue.
Aujourd’hui, la standardisation est un pilier essentiel des systèmes de production modernes, intégrant des technologies avancées et des outils numériques pour renforcer l’efficacité et la qualité. Les entreprises françaises, en particulier, adoptent de plus en plus ces pratiques pour rester compétitives sur le marché mondial.
Avantages de la Standardisation dans la Production
Amélioration de la Qualité des Produits
La standardisation permet d’établir des normes claires et cohérentes pour chaque étape du processus de production. En suivant des procédures standardisées, les entreprises peuvent garantir que chaque produit respecte les mêmes critères de qualité, réduisant ainsi les variations et les défauts. Cela conduit à une amélioration significative de la qualité des produits finis, ce qui est crucial pour maintenir la satisfaction des clients et renforcer la réputation de l’entreprise.
Réduction des Coûts de Production
En minimisant les variations et en optimisant les processus, la standardisation contribue à réduire les coûts de production. Les entreprises peuvent diminuer les pertes de matières premières, réduire les temps de cycle et limiter les interruptions de production. De plus, en éliminant les gaspillages et en rationalisant les opérations, la standardisation permet d’utiliser les ressources de manière plus efficace, ce qui se traduit par des économies substantielles.
Augmentation de l’Efficacité et de la Productivité
La mise en œuvre de procédures standardisées permet d’optimiser les flux de travail et de réduire les temps morts. Les opérateurs connaissent exactement les étapes à suivre et les méthodes à appliquer, ce qui augmente la fluidité et la rapidité des processus. Cette augmentation de l’efficacité se traduit par une productivité accrue, permettant aux usines de produire plus en moins de temps tout en maintenant une qualité constante.
Renforcement de la Sécurité au Travail
La standardisation inclut également des procédures de sécurité qui garantissent que les employés suivent des pratiques sécuritaires à chaque étape de la production. En ayant des standards clairs, les risques d’accidents et de blessures sont réduits. Les employés sont mieux informés des dangers potentiels et des mesures de prévention, ce qui crée un environnement de travail plus sûr. Cela conduit à une réduction des coûts liés aux accidents du travail et surtout à une amélioration du bien-être des employés.
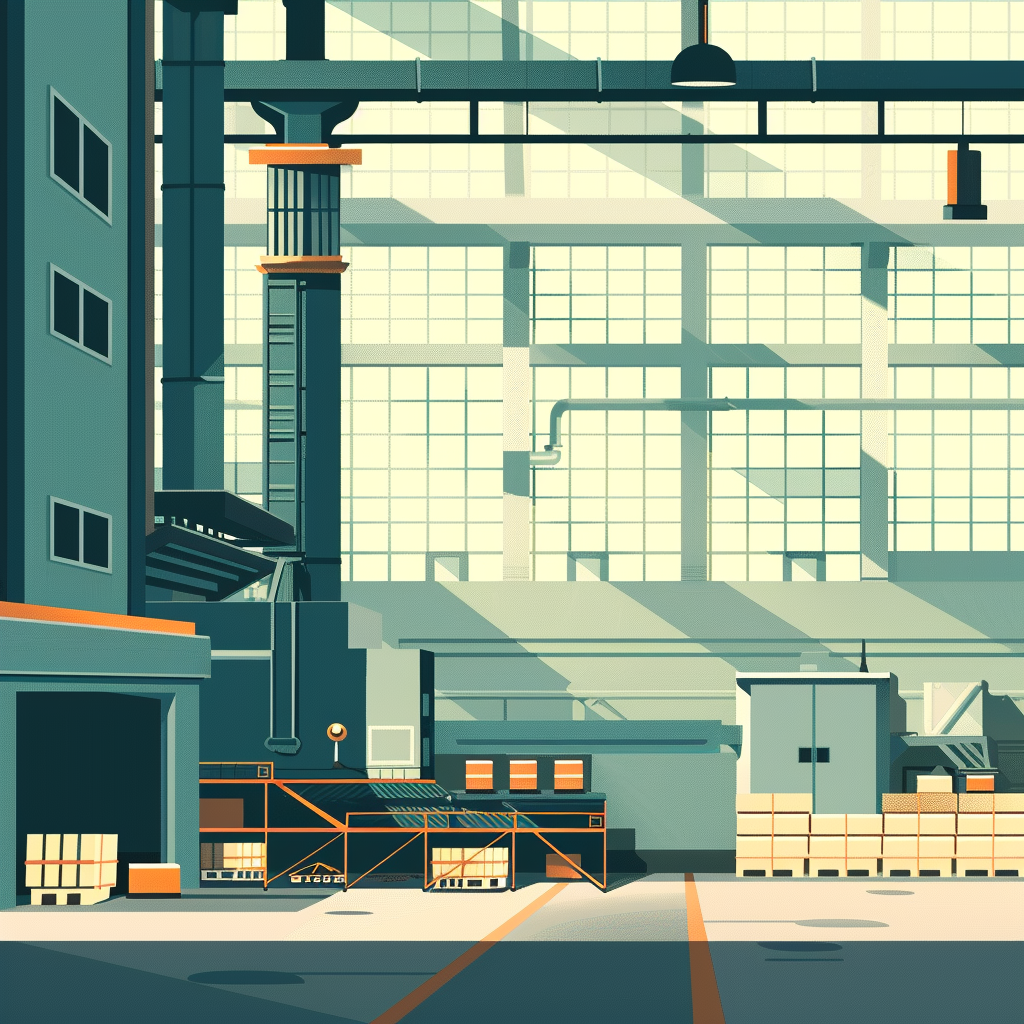
Outils et Méthodes de Standardisation
SOP (Standard Operating Procedures) et Standard work
Les SOP, ou procédures opérationnelles standardisées, sont des documents qui détaillent les étapes nécessaires pour accomplir une tâche de manière cohérente et uniforme. Elles sont essentielles pour garantir que chaque opérateur exécute les processus de la même manière, réduisant ainsi les variations et les erreurs. Les SOP sont souvent accompagnées de visuels ou de diagrammes pour faciliter la compréhension et l’application.
On parle également souvent de standard de travail, standard au poste ou standard work. L’idée étant que la meilleure manière d’effectuer une tâche à ce jour est définie, et doit donc être enseignée à chaque personne pour optimiser l’implémentation de cette tâche. Il inclut généralement des instructions claires et précises, des temps de cycle, et des points de contrôle pour assurer que le travail est effectué de manière uniforme et efficace.
5S
La méthode 5S est un système d’organisation du lieu de travail qui vise à améliorer l’efficacité et la sécurité. Les 5S représentent :
- Seiri (Trier) : Éliminer les éléments inutiles de l’espace de travail.
- Seiton (Ranger) : Organiser les outils et les matériaux pour un accès facile.
- Seiso (Nettoyer) : Maintenir le lieu de travail propre et ordonné.
- Seiketsu (Standardiser) : Établir des normes pour les tâches et le nettoyage.
- Shitsuke (Maintenir/Suivre) : Maintenir la discipline et suivre les standards.
En appliquant les 5S, les entreprises peuvent réduire les pertes de temps, améliorer la sécurité et augmenter la productivité.
Gemba Walks
Les gemba walks sont des outils simples mais puissants pour s’assurer que toutes les étapes d’un processus sont suivies correctement. Elles aident à éviter les oublis et les erreurs, surtout dans des environnements de production complexes. Les gemba walks peuvent être utilisées pour des inspections de qualité, des contrôles de sécurité, ou pour vérifier l’achèvement de tâches spécifiques.
L’exécution des gemba walks doit d’ailleurs être améliorée et standardisée afin d’auditer un processus de la meilleure manière. Vous retrouverez ce genre d’outils dans des solutions digitales comme Shizen par exemple, qui permet d’effectuer son gemba walk en suivant un processus clair. Les données issues du gemba walk sont ensuite consolidées pour être suivies en AIC, ou à un autre niveau de management.
Management Visuel
Le management visuel utilise des signaux visuels pour communiquer rapidement des informations importantes. Cela inclut l’utilisation de tableaux de bord, de graphiques de performance, et de codes couleurs pour indiquer l’état des processus ou des équipements. Le management visuel aide à identifier rapidement les anomalies et à prendre des mesures correctives immédiates.
C’est un des autres avantages de l’utilisation d’une solution digitale comme Shizen qui offre des managements visuels sur mesure, dans lesquels vous retrouvez les informations issues des gemba walks, des résolutions de problèmes, etc.
Comment Utiliser ces Outils pour Créer des Standards Efficaces
Pour créer des standards efficaces, il est crucial de :
- Impliquer les Opérateurs : Les personnes qui exécutent les tâches au quotidien doivent être impliquées dans la création des standards pour s’assurer qu’ils sont pratiques et applicables.
- Documenter et Communiquer : Toutes les procédures standardisées doivent être clairement documentées et facilement accessibles à tous les employés concernés.
- Former et Sensibiliser : Les employés doivent recevoir une formation adéquate sur les nouveaux standards et comprendre leur importance pour la qualité et l’efficacité.
- Réviser et Améliorer : Les standards doivent être régulièrement révisés et améliorés en fonction des retours d’expérience et des changements dans les processus ou les technologies.
Enfin, comme évoqué précédemment, il est tout à fait possible d’accompagner la démarche d’une solution digitale globale. C’est ce que Toyota a choisi de faire en mettant en place la solution Shizen sur la totalité de son usine française :
Mise en Œuvre de la Standardisation dans une Usine
Étapes pour Développer et Mettre en Place des Standards dans une Usine
- Analyse des Processus Actuels : La première étape consiste à examiner et documenter les processus actuels pour identifier les variations et les inefficacités. Cela permet de déterminer les domaines qui bénéficieraient le plus de la standardisation. Le VSM est un outil très utile pour ce genre d’usage.
- Développement des Standards : En collaboration avec les opérateurs et les responsables de production, développez des procédures standardisées détaillées pour chaque processus clé. Ces standards doivent inclure des instructions précises, des temps de cycle, et des critères de qualité.
- Validation des Standards : Testez les nouvelles procédures dans des conditions réelles pour s’assurer qu’elles sont pratiques et efficaces. Recueillez les retours des opérateurs, ils sont vos meilleurs alliés dans cette démarche, et ajustez les standards si nécessaire.
- Documentation et Communication : Documentez les standards de manière claire et accessible, en utilisant des visuels et des diagrammes pour faciliter la compréhension. Assurez-vous que tous les employés concernés ont accès à ces documents et les comprennent.
- Formation et Sensibilisation des Employés : Organisez des sessions de formation pour expliquer les nouveaux standards, leur importance, et comment les appliquer correctement. La sensibilisation à l’importance de la standardisation aide à garantir l’adhésion des employés.
- Mise en Œuvre et Suivi : Implémentez les standards dans la production quotidienne et suivez leur application. Utilisez des audits réguliers pour vérifier la conformité et identifier les améliorations possibles. Utilisez un DMS pour plus de facilité et de pérennité.
Rôles et Responsabilités des Différents Acteurs
- Opérateurs : Ils doivent suivre les procédures standardisées et fournir des retours sur leur efficacité. Vous allez probablement changer leurs méthodes de travail, procédez donc avec tact. Ils peuvent être des moteurs exceptionnels de la démarche.
- Managers : Ils sont responsables de la supervision de la mise en œuvre des standards et de l’encouragement à l’amélioration continue. Les managers soutiennent mais ils doivent également être soutenus par le support et la direction.
- Équipes de Qualité : Elles doivent surveiller la conformité aux standards et coordonner les audits réguliers pour assurer une application correcte.
Comment Mesurer l’Impact de la Standardisation sur la Performance de l’Usine
Mesurer l’impact de la standardisation nécessite la mise en place d’indicateurs de performance clés (KPIs). Ces indicateurs peuvent inclure :
- Taux de Défectuosité : Mesure des produits défectueux avant et après la mise en œuvre des standards.
- Temps de Cycle : Comparaison des temps de cycle de production pour identifier les gains d’efficacité.
- Productivité des Employés : Évaluation des changements dans la productivité des opérateurs.
- Incidents de Sécurité : Suivi des incidents de sécurité pour évaluer l’impact des standards sur la sécurité au travail, avec une croix sécurité par exemple.
Indicateurs de Performance Clés (KPIs) à Suivre pour Évaluer l’Efficacité des Standards
- Conformité aux Standards : Pourcentage d’opérations conformes aux standards établis.
- Réduction des Variations : Écart-type des processus avant et après la standardisation.
- Satisfaction des Employés : Feedback des employés concernant les nouveaux standards.
- Efficacité Globale de l’Équipement (OEE) : Mesure de la performance des équipements en fonction des standards.
Conclusion
La standardisation est un levier puissant pour optimiser les processus de production dans le secteur industriel. En établissant des normes et des procédures uniformes, les usines peuvent garantir une qualité constante, réduire les coûts, augmenter la productivité et renforcer la sécurité au travail. Pour les usines françaises, la mise en œuvre de pratiques de standardisation est cruciale pour rester compétitives.
Les outils et méthodes de standardisation tels que les SOP, le 5S, les Gemba walks et le management visuel sont essentiels pour créer des standards efficaces. Leur utilisation permet non seulement d’améliorer l’efficacité opérationnelle mais aussi de favoriser une culture d’amélioration continue.
L’implémentation de la standardisation dans une usine nécessite une approche structurée impliquant tous les acteurs, des opérateurs aux managers et équipes de qualité. La formation, la communication et l’engagement des employés sont des facteurs clés de succès. Mesurer l’impact de la standardisation à travers des indicateurs de performance clés permet de suivre les progrès et de continuer à optimiser les processus.
En conclusion, la standardisation est une pratique incontournable pour les gestionnaires d’usine qui souhaitent améliorer continuellement leurs opérations. Adopter une approche standardisée, soutenue par des outils numériques comme ceux proposés par Shizen, peut transformer les performances industrielles et garantir une compétitivité durable.