Le 5S est une méthode qui vise à optimiser l’espace de travail, à réduire les gaspillages, à augmenter la qualité et à améliorer la sécurité. Elle repose sur cinq étapes clés, dont les noms commencent par la lettre S : Seiri (Trier), Seiton (Ranger), Seiso (Nettoyer), Seiketsu (Standardiser) et Shitsuke (Maintenir). Le 5S fait partie du lean management, une démarche d’amélioration continue inspirée du système de production Toyota.
Dans cet article, nous allons vous expliquer ce qu’est le 5S, comment il se compose, comment il s’applique et quels sont ses avantages. Nous vous donnerons également des conseils pour mettre en œuvre le 5S dans votre entreprise.
Introduction à la méthode 5S
Définition de la méthode 5S
Le 5S est une méthode qui permet d’organiser le lieu de travail de manière à ce qu’il soit propre, ordonné, sécurisé et adapté aux besoins des opérateurs. Le 5S vise à éliminer les éléments inutiles, à ranger les objets utiles, à nettoyer l’environnement, à standardiser les règles et à maintenir les bonnes pratiques. Le 5S favorise ainsi l’efficacité opérationnelle, la qualité des produits ou services, la satisfaction des clients et des employés, et la culture lean.
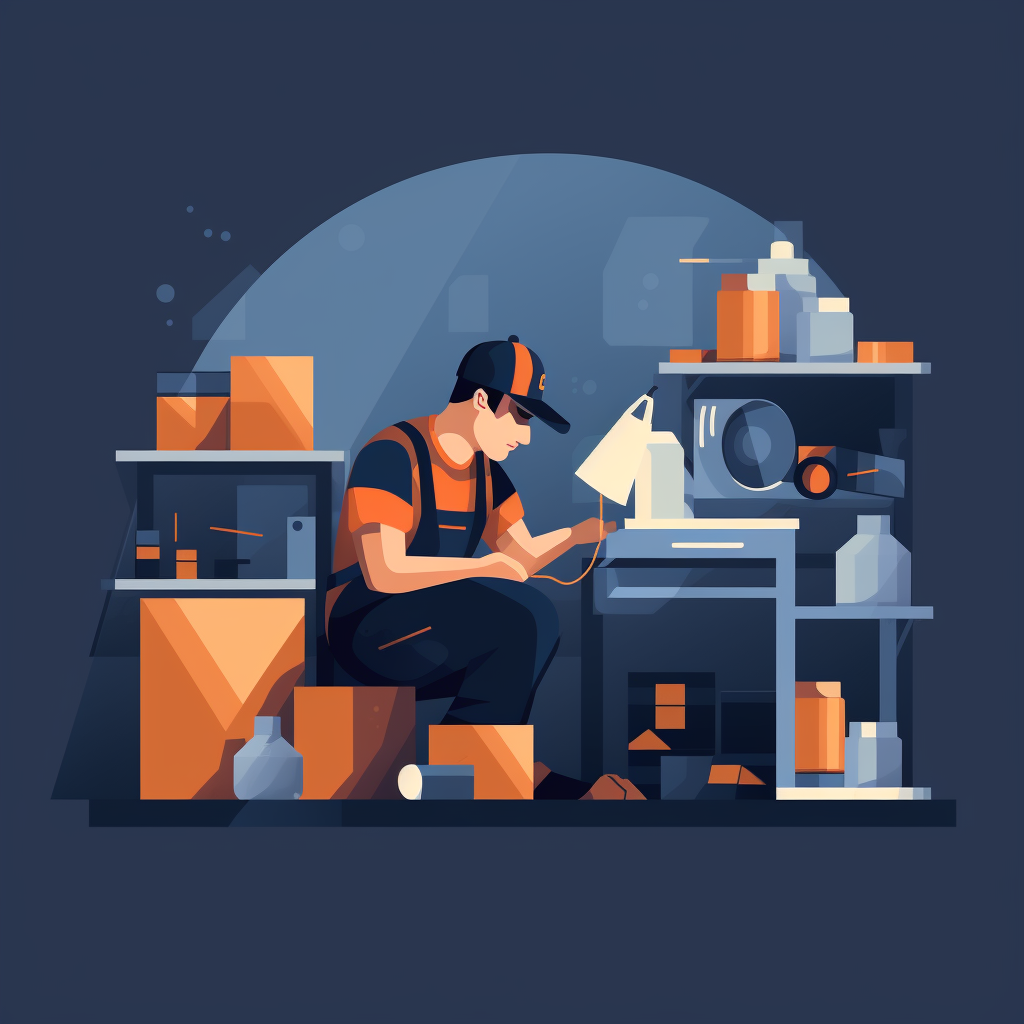
Histoire et origine de la méthode 5S
Le 5S est né au Japon dans les années 1950, dans le cadre du développement du système de production Toyota (TPS). Le TPS est un modèle de gestion qui repose sur l’élimination des gaspillages (muda), des irrégularités (mura) et des surcharges (muri). Le TPS s’appuie sur des principes tels que le juste-à-temps (JIT), le jidoka (autonomation) ou le kaizen (amélioration continue). Le 5S est l’un des outils du TPS, qui permet de créer un environnement de travail propice à la performance et à l’innovation. Le nom 5S vient des cinq mots japonais qui désignent les étapes de la méthode : seiri, seiton, seiso, seiketsu et shitsuke.
Composantes de la méthode 5S
Seiri (Trier)
La première étape du 5S consiste à trier les objets présents sur le lieu de travail et à éliminer ceux qui sont inutiles ou superflus. L’objectif est de ne garder que ce qui est nécessaire au processus de production ou au service rendu. Le tri permet de libérer de l’espace, de faciliter l’accès aux outils, de réduire les coûts et les risques d’erreur ou d’accident.
Seiton (Ranger)
La deuxième étape du 5S consiste à ranger les objets utiles de manière logique et ergonomique. L’objectif est de faciliter leur repérage, leur utilisation et leur remise en place. Le rangement implique de définir des emplacements précis pour chaque objet, de les identifier clairement par des étiquettes ou des codes couleur, et de respecter l’ordre établi. Le rangement permet d’améliorer la fluidité du travail, de gagner du temps et d’éviter les pertes ou les détériorations.
Seiso (Nettoyer)
La troisième étape du 5S consiste à nettoyer régulièrement le lieu de travail et les équipements utilisés. L’objectif est d’assurer la propreté et l’hygiène du poste de travail, ainsi que le bon fonctionnement des machines. Le nettoyage implique de définir des fréquences et des responsabilités pour chaque tâche, de vérifier l’état des outils et de signaler les anomalies ou les dysfonctionnements. Le nettoyage permet d’améliorer la qualité du travail, de prévenir les pannes ou les accidents, et de renforcer le sentiment d’appartenance.
Seiketsu (Standardiser)
La quatrième étape du 5S consiste à standardiser les règles et les procédures relatives aux trois premières étapes. L’objectif est d’harmoniser les pratiques et de garantir leur application par tous les employés. La standardisation implique de définir des normes et des indicateurs pour chaque activité, de les documenter et de les diffuser, et de les contrôler régulièrement. La standardisation permet d’améliorer la fiabilité du travail, de faciliter la communication et la formation, et de favoriser le management visuel.
Shitsuke (Maintenir)
La cinquième étape du 5S consiste à maintenir les résultats obtenus grâce aux quatre premières étapes, et à chercher à les améliorer en permanence. L’objectif est de pérenniser la méthode 5S et d’en faire une habitude pour tous les employés. Le maintien implique de sensibiliser et de former le personnel au 5S, de le motiver et de le récompenser, et de l’impliquer dans la résolution des problèmes et la proposition d’améliorations. Le maintien permet d’améliorer la performance globale de l’entreprise, de développer la culture lean et l’excellence opérationnelle.
Applications de la méthode 5S
Utilisation du 5S dans l’industrie manufacturière
Le 5S est une méthode qui s’applique principalement dans l’industrie manufacturière, où elle permet d’optimiser l’utilisation des moyens de production, tels que les machines, les outils ou les matières premières. Le 5S contribue à réduire les temps de cycle, les stocks, les rebuts, les retouches ou les arrêts. Le 5S favorise également la qualité des produits fabriqués, en évitant les défauts ou les non-conformités. Le 5S améliore enfin la sécurité des opérateurs, en prévenant les accidents du travail ou les maladies professionnelles.
Le rôle du 5S dans l’amélioration continue
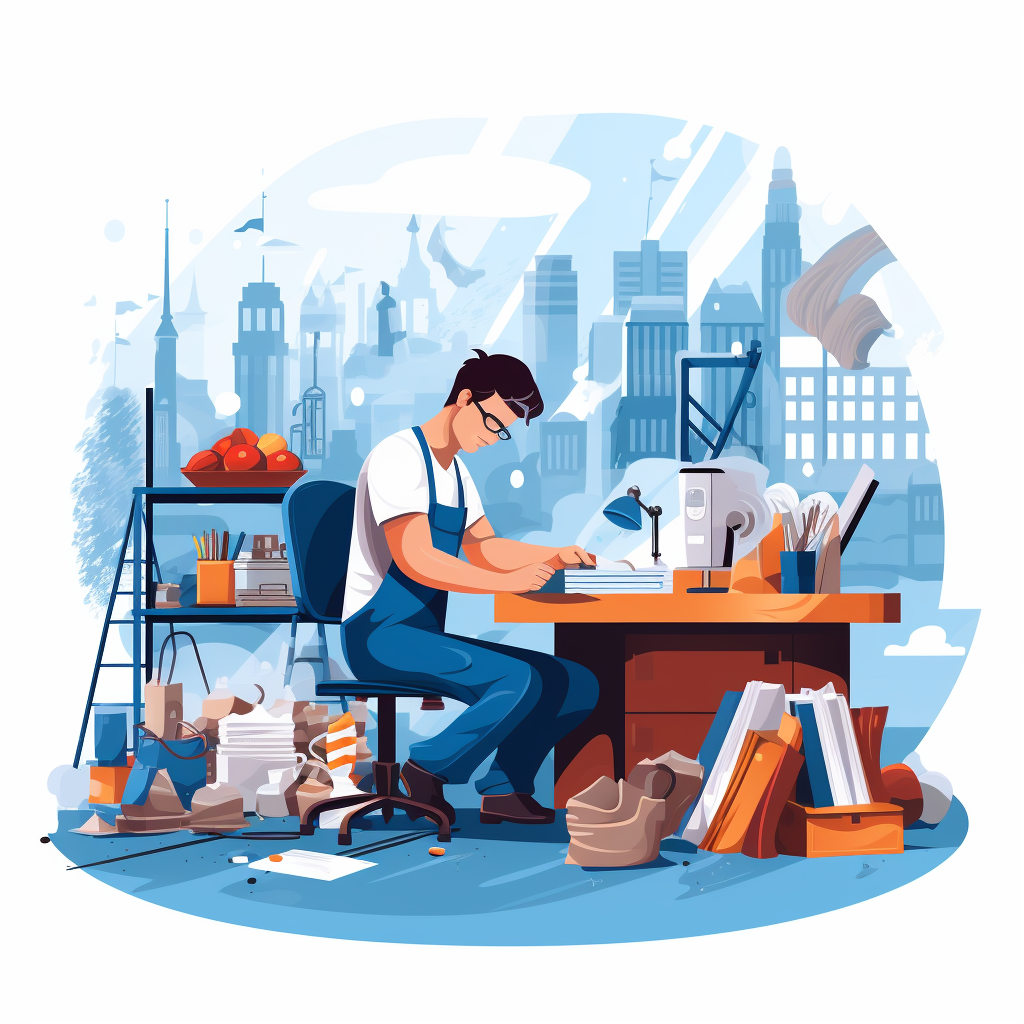
Le 5S est une méthode qui s’inscrit dans une démarche d’amélioration continue, qui vise à augmenter la valeur ajoutée pour le client tout en réduisant les gaspillages. Le 5S est un outil qui permet de mettre en place les conditions nécessaires à l’amélioration continue, en créant un environnement de travail propice à l’innovation et à la résolution des problèmes.
Le 5S est également un préalable à l’utilisation d’autres outils d’amélioration continue, tels que le value stream mapping (VSM), qui permet de cartographier le flux de valeur d’un processus, ou le kaizen, qui permet d’impliquer le personnel dans la recherche de solutions.
Exemples concrets d’application du 5S
Le 5S est une méthode qui peut s’appliquer à tout type d’activité ou de secteur. Voici quelques exemples concrets d’application du 5S :
- Dans un atelier mécanique, le 5S a permis de réduire le temps de recherche des outils de 15 minutes à 30 secondes par jour et par opérateur, en éliminant les outils inutiles, en créant des panneaux muraux avec des emplacements dédiés pour chaque outil, et en instaurant un système d’étiquetage et de vérification.
- Dans un service administratif, le 5S a permis de réduire le volume des documents papier de 80%, en triant les documents nécessaires et en numérisant ceux qui pouvaient l’être, en rangeant les documents restants dans des classeurs identifiés par des codes couleur, et en nettoyant régulièrement le bureau.
- Dans un hôpital, le 5S a permis de réduire les infections nosocomiales de 50%, en triant et en désinfectant le matériel médical, en rangeant les médicaments et les dispositifs dans des armoires sécurisées, et en nettoyant et en standardisant les procédures d’hygiène.
Le 5S est parfaitement adapté dans une animation de la performance régulière.
Avantages de la mise en place de la méthode 5S
Amélioration de l’efficacité opérationnelle
Le 5S est une méthode qui permet d’améliorer l’efficacité opérationnelle, c’est-à-dire la capacité à produire plus et mieux avec moins de ressources. Le 5S permet de réduire les gaspillages, tels que les mouvements inutiles, les transports excessifs, les attentes, les surproductions, les stocks, les défauts ou les surqualités. Le 5S permet également d’augmenter la productivité, la flexibilité et la réactivité du processus de production ou du service rendu. Le 5S contribue ainsi à accroître la compétitivité et la rentabilité de l’entreprise.
Augmentation de la sécurité au travail
Le 5S est une méthode qui permet d’augmenter la sécurité au travail, c’est-à-dire la prévention des risques professionnels liés à l’activité exercée. Le 5S permet de réduire les sources de danger, telles que les objets coupants, les produits chimiques, les câbles électriques, les machines défectueuses ou les espaces encombrés. Le 5S permet également derenforcer la vigilance, la responsabilité et le respect des consignes de sécurité par les employés. Le 5S contribue ainsi à diminuer le nombre et la gravité des accidents du travail ou des maladies professionnelles. Utilisez-le dans le cadre de tournées terrain régulières dans votre environnement de travail.
Amélioration de l’organisation du lieu de travail
Le 5S est une méthode qui permet d’améliorer l’organisation du lieu de travail, c’est-à-dire la disposition et l’agencement des éléments qui composent l’espace de travail. Le 5S permet de créer un environnement de travail propre, ordonné, fonctionnel et agréable. Le 5S permet également de faciliter la communication, la collaboration et l’apprentissage entre les employés. Le 5S contribue ainsi à améliorer le climat social, la motivation et la satisfaction au travail.
Étapes pour la mise en place de la méthode 5S
Identification des besoins et objectifs
La première étape pour mettre en place le 5S consiste à identifier les besoins et les objectifs de l’entreprise. Il s’agit de faire un diagnostic de la situation actuelle du lieu de travail, en évaluant ses forces et ses faiblesses, ses opportunités et ses menaces. Il s’agit également de définir les attentes et les exigences des clients internes et externes, ainsi que les contraintes légales ou réglementaires. Il s’agit enfin de fixer des objectifs SMART (Spécifiques, Mesurables, Atteignables, Réalistes et Temporels) pour chaque zone ou processus concerné par le 5S.
Implémentation des 5 stages
La deuxième étape pour mettre en place le 5S consiste à implémenter les cinq étapes de la méthode : Seiri (Trier), Seiton (Ranger), Seiso (Nettoyer), Seiketsu (Standardiser) et Shitsuke (Maintenir). Il s’agit de suivre un plan d’action détaillé pour chaque étape, en définissant les tâches à réaliser, les responsables à désigner, les ressources à mobiliser, les délais à respecter et les résultats à mesurer. Il s’agit également d’impliquer le personnel dans la mise en œuvre du 5S, en le formant, en le consultant et en le reconnaissant.
Maintien et amélioration continue
La troisième étape pour mettre en place le 5S consiste à maintenir et à améliorer les résultats obtenus grâce aux cinq étapes de la méthode. Il s’agit de contrôler régulièrement le respect des normes et des procédures établies, en utilisant des outils tels que les audits, les check-lists ou les tableaux de bord. Il s’agit également de chercher en permanence des opportunités d’amélioration, en utilisant des outils tels que le PDCA (Plan-Do-Check-Act), le brainstorming ou le benchmarking. L’implémentation d’indicateurs de performance vous permettra de mieux connaître la réalité du terrain. Il s’agit enfin de pérenniser la méthode 5S, en la faisant évoluer avec les besoins et les objectifs de l’entreprise.
Challenges pendant l’implémentation de la méthode 5S
Résistance au changement
L’un des principaux challenges pendant l’implémentation de la méthode 5S est la résistance au changement. Il s’agit du phénomène par lequel les employés se montrent réticents ou hostiles à l’idée de modifier leurs habitudes ou leurs pratiques de travail. La résistance au changement peut avoir plusieurs causes, telles que la peur de l’inconnu, la perte de repères, la remise en cause des compétences, le manque d’information ou de participation, ou encore la défiance vis-à-vis du management. La résistance au changement peut avoir plusieurs conséquences, telles que le ralentissement du projet, la baisse de la qualité du travail, le conflit ou le turnover.
Maintenir l’engagement
Un autre challenge pendant l’implémentation de la méthode 5S est de maintenir l’engagement du personnel. Il s’agit du phénomène par lequel les employés se montrent motivés et impliqués dans la réussite du projet. L’engagement du personnel peut être difficile à obtenir et à conserver, notamment si le projet est long, complexe ou incertain. L’engagement du personnel peut être favorisé par plusieurs facteurs, tels que la communication, la formation, la participation, la reconnaissance ou la récompense.
Assurer un suivi rigoureux
Un troisième challenge pendant l’implémentation de la méthode 5S est d’assurer un suivi rigoureux du projet. Il s’agit du processus par lequel le management vérifie et évalue l’avancement et les résultats du projet, en comparant les objectifs fixés et les réalisations effectives. Le suivi rigoureux du projet peut être compliqué à mettre en place et à maintenir, notamment si le projet est dispersé, diversifié ou dynamique. Le suivi rigoureux du projet peut être facilité par plusieurs moyens, tels que les indicateurs, les rapports, les réunions ou les audits.
Conclusion
Récapitulation des points importants
Pour conclure, nous pouvons récapituler les points importants de cet article sur le 5S :
- Le 5S est une méthode d’organisation et d’amélioration du lieu de travail, qui repose sur cinq étapes : Seiri (Trier), Seiton (Ranger), Seiso (Nettoyer), Seiketsu (Standardiser) et Shitsuke (Maintenir).
- Le 5S fait partie du lean management, une démarche d’amélioration continue inspirée du système de production Toyota.
- Le 5S permet d’améliorer l’efficacité opérationnelle, la sécurité au travail et l’organisation du lieu de travail.
- Le 5S peut s’appliquer à tout type d’activité ou de secteur.
- Le 5S nécessite une identification des besoins et objectifs, une implémentation des cinq étapes et un maintien et une amélioration continue.
- Le 5S présente des challenges tels que la résistance au changement, le maintien de l’engagement et l’assurance d’un suivi rigoureux.
Perspective pour l’avenir du 5S
Pour terminer, nous pouvons donner une perspective pour l’avenir du 5S. Le 5S est une méthode qui a fait ses preuves depuis plus de 70 ans dans le monde entier dans le monde entier, et qui continue à s’adapter aux évolutions technologiques, économiques et sociales. Le 5S est une méthode qui peut être complétée par d’autres outils ou méthodes, tels que le 6S (qui ajoute la notion de sécurité), le 7S (qui ajoute la notion de satisfaction), le 8S (qui ajoute la notion de stratégie) ou encore le 5R (qui remplace les mots japonais par des mots français : Réduire, Ranger, Rendre propre, Rendre évident, Respecter).
Le 5S est une méthode qui peut être appliquée à d’autres domaines que le lieu de travail, tels que la maison, l’école ou la vie personnelle. Le 5S est une méthode qui peut contribuer à un développement durable, en réduisant l’impact environnemental et en favorisant le bien-être social.
Nous espérons que cet article vous a permis de mieux comprendre ce qu’est le 5S, comment il fonctionne, comment il s’applique et quels sont ses bénéfices. Si vous souhaitez mettre en œuvre le 5S dans votre entreprise ou dans votre vie personnelle, n’hésitez pas à nous contacter pour bénéficier de nos services de rédaction SEO, de formation ou de conseil. Nous vous accompagnerons dans votre démarche d’amélioration continue et d’excellence opérationnelle.