Vous avez sûrement entendu parler de la méthode Kaizen, cette philosophie japonaise qui vise à améliorer continuellement les processus et les systèmes dans les entreprises. Mais savez-vous ce que signifie réellement le mot kaizen, quels sont ses principes de base, comment il s’applique à l’industrie et quels sont ses avantages ? Dans cet article, nous allons vous expliquer tout ce que vous devez savoir sur la méthode Kaizen et son rôle clé dans l’industrie.
Définition de la méthode Kaizen
Qu’est-ce que la méthode Kaizen ?
Kaizen est un mot japonais qui signifie « changement pour le mieux » ou « amélioration ». Il se compose de deux caractères : kai, qui signifie « changement », et zen, qui signifie « bien » . La méthode Kaizen est donc une approche qui consiste à rechercher constamment des améliorations dans les processus, les produits, les services et la culture d’entreprise . La méthode Kaizen repose sur l’idée que de petits changements progressifs peuvent avoir un impact important à long terme.
Les principes de base de la méthode Kaizen
La méthode Kaizen repose sur quelques principes fondamentaux :
- L’amélioration est l’affaire de tous : du PDG aux employés de la chaîne de production, tout le monde doit être impliqué et engagé dans la recherche d’améliorations.
- L’amélioration est continue : il ne s’agit pas d’un projet ponctuel ou d’un objectif à atteindre, mais d’un processus permanent qui vise à s’adapter aux besoins des clients et aux évolutions du marché.
- L’amélioration est basée sur les faits : il faut mesurer les performances actuelles, identifier les problèmes, analyser les causes, proposer des solutions, les tester, les évaluer et les standardiser.
- L’amélioration est centrée sur le client : il faut se mettre à la place du client, comprendre ses attentes, ses besoins, ses problèmes et ses satisfactions, et chercher à lui offrir la meilleure valeur possible.
- L’amélioration est orientée vers le processus : il faut se focaliser sur les causes des problèmes plutôt que sur leurs conséquences, et chercher à optimiser le flux de travail, à réduire les gaspillages et à augmenter la qualité.
Le concept de l’amélioration continue
Le concept de l’amélioration continue est au cœur de la méthode Kaizen. Il s’agit d’un cycle qui se répète sans fin et qui suit quatre étapes :
- Planifier : définir les objectifs, identifier les problèmes, analyser les données, proposer des solutions.
- Faire : mettre en œuvre les solutions, réaliser des tests, collecter des données.
- Vérifier : comparer les résultats obtenus avec les objectifs fixés, évaluer l’efficacité des solutions, identifier les points forts et les points faibles.
- Agir : standardiser les solutions qui fonctionnent, corriger ou améliorer celles qui ne fonctionnent pas, communiquer les résultats, célébrer les succès.
Ce cycle est aussi appelé PDCA (Plan-Do-Check-Act) ou roue de Deming, du nom du célèbre expert en gestion de la qualité qui a popularisé ce modèle.
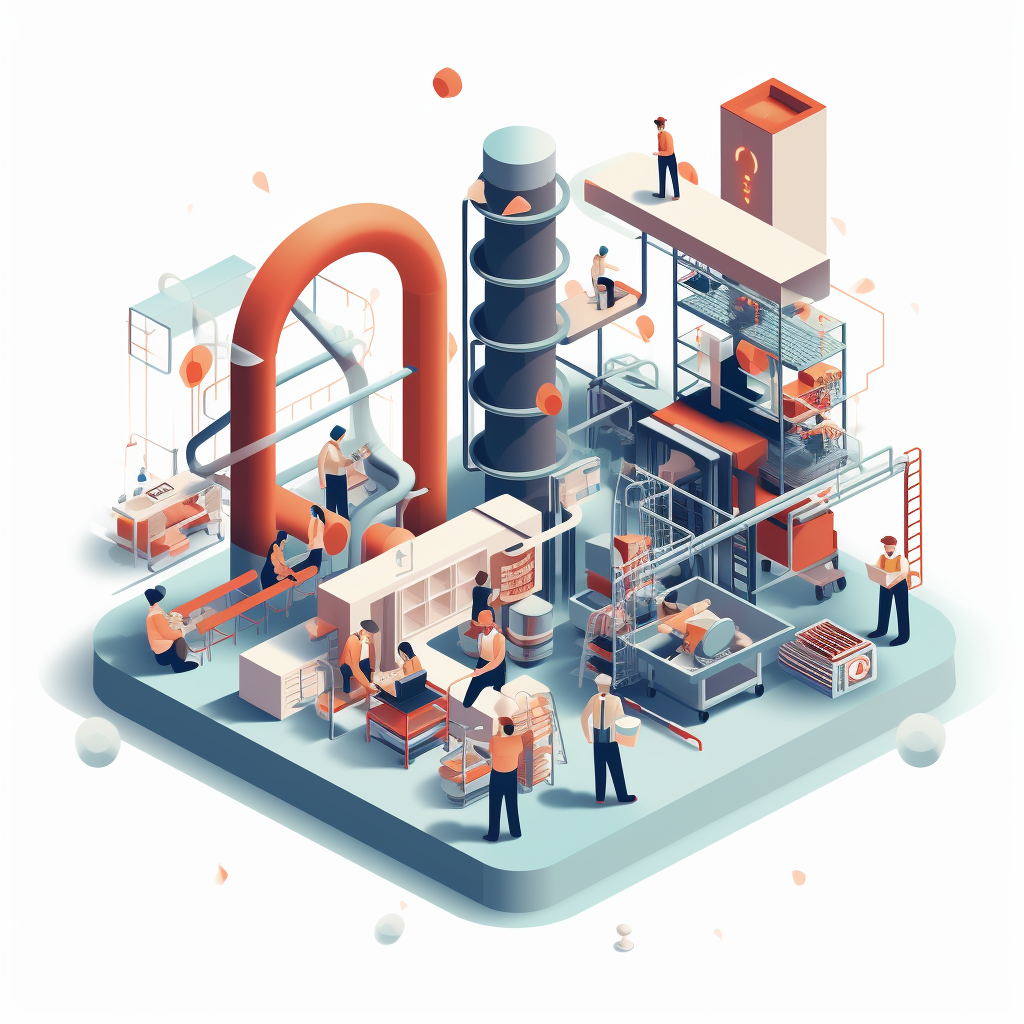
La pertinence du Kaizen dans l’industrie
La méthode Kaizen au service de la productivité
La méthode Kaizen est particulièrement adaptée au secteur industriel, où la productivité est un facteur clé de compétitivité. En effet, en appliquant la méthode Kaizen, les entreprises industrielles peuvent améliorer leur efficacité, leur flexibilité et leur réactivité, tout en réduisant leurs coûts et leurs délais. La méthode Kaizen permet notamment de :
- Optimiser l’utilisation des ressources : matériel, personnel, énergie, espace, etc.
- Améliorer la qualité des produits et des services : réduire les défauts, les erreurs, les retours, les réclamations, etc.
- Augmenter la satisfaction des clients : répondre à leurs besoins, leurs attentes, leurs exigences, etc.
- Renforcer la motivation des employés : les impliquer, les responsabiliser, les former, les récompenser, etc.
La gestion du flux de travail avec Kaizen
La méthode Kaizen permet également de gérer efficacement le flux de travail dans l’industrie. Il s’agit d’optimiser le processus de production en éliminant les sources de variation, de perturbation et d’attente. La méthode Kaizen s’appuie sur des outils tels que :
- Le 5S : une technique qui vise à organiser l’espace de travail en cinq étapes : trier, ranger, nettoyer, standardiser et maintenir.
- Le SMED : une technique qui vise à réduire le temps de changement de série ou de format en séparant les opérations internes (qui nécessitent l’arrêt de la machine) et externes (qui peuvent être réalisées pendant que la machine fonctionne).
- Le Kanban : une technique qui vise à réguler le flux de production en fonction de la demande du client, en utilisant des cartes ou des signaux visuels qui indiquent le besoin de réapprovisionnement ou de production.
- Le Poka-Yoké : une technique qui vise à prévenir les erreurs humaines en utilisant des dispositifs ou des systèmes qui empêchent ou signalent les défauts potentiels.
La réduction du gaspillage grâce à Kaizen
La méthode Kaizen permet aussi de réduire le gaspillage dans l’industrie. Il s’agit d’éliminer tout ce qui n’apporte pas de valeur ajoutée au client ou au produit. La méthode Kaizen s’inspire du concept de lean management, qui identifie sept types de gaspillage :
- La surproduction : produire plus que nécessaire ou avant que ce soit nécessaire.
- L’attente : perdre du temps à attendre que quelque chose se produise ou que quelqu’un agisse.
- Le transport : déplacer inutilement des produits ou des matériaux d’un endroit à un autre.
- L’inventaire : stocker trop de produits ou de matériaux qui ne sont pas utilisés immédiatement.
- Le mouvement : effectuer des gestes inutiles ou inefficaces lors du processus de production.
- Le surtraitement : réaliser des opérations qui n’apportent pas de valeur au client ou au produit.
- Les défauts : produire des produits ou des services non conformes aux attentes du client.
La mise en œuvre de la méthode Kaizen dans l’industrie
Étapes essentielles de la mise en œuvre de Kaizen
Pour mettre en œuvre la méthode Kaizen dans l’industrie, il faut suivre quelques étapes essentielles :
- Faire un diagnostic initial : évaluer la situation actuelle, identifier les forces et les faiblesses, définir les indicateurs clés de performance.
- Fixer des objectifs SMART : spécifiques, mesurables, atteignables, réalistes et temporellement définis.
- Élaborer un plan d’action : déterminer les actions à mener, les responsables, les ressources, les délais, les coûts, etc.
- Mettre en œuvre le plan d’action : réaliser les actions prévues, suivre les indicateurs, collecter les données, communiquer les résultats.
- Contrôler et ajuster le plan d’action : vérifier si les objectifs sont atteints, identifier les écarts, analyser les causes, apporter des corrections ou des améliorations.
- Pérenniser et diffuser le plan d’action : standardiser les bonnes pratiques, former le personnel, partager les expériences, célébrer les succès.
Challenges et obstacles communs et comment les surmonter
La mise en œuvre de la méthode Kaizen dans l’industrie n’est pas sans difficultés. Il existe plusieurs challenges et obstacles communs qui peuvent freiner ou compromettre la réussite du projet. Voici quelques exemples et comment les surmonter :
- La résistance au changement : certaines personnes peuvent être réticentes à changer leurs habitudes de travail, à adopter de nouvelles méthodes ou à remettre en question leurs pratiques. Pour y faire face, il faut impliquer le personnel dès le début du projet, expliquer les raisons et les bénéfices du changement, écouter leurs besoins et leurs suggestions, et les accompagner dans la transition.
- Le manque de temps : certaines personnes peuvent considérer que la méthode Kaizen est trop chronophage, qu’elle demande trop d’efforts ou qu’elle détourne de leur activité principale. Pour y faire face, il faut planifier le projet de manière réaliste, définir des priorités, allouer des ressources suffisantes, et montrer les gains de temps et d’efficacité à long terme.
- Le manque de compétences : certaines personnes peuvent se sentir dépassées par la complexité ou la nouveauté des outils ou des techniques utilisés dans la méthode Kaizen. Pour y faire face, il faut former le personnel aux méthodes et aux outils utilisés, leur fournir des supports et des guides, et leur proposer un accompagnement personnalisé.
- Le manque de suivi : certaines personnes peuvent perdre de vue les objectifs du projet, négliger les indicateurs ou oublier de communiquer les résultats. Pour y faire face, il faut mettre en place un système de suivi régulier, désigner un responsable du projet, organiser des réunions et des rapports périodiques, et valoriser les progrès et les réussites.
Importance de la culture d’entreprise dans la réussite de Kaizen
La méthode Kaizen n’est pas seulement une méthode technique ou opérationnelle. C’est aussi une méthode qui repose sur une culture d’entreprise spécifique. En effet, pour réussir à mettre en œuvre la méthode Kaizen dans l’industrie, il faut instaurer une culture d’entreprise qui favorise :
- L’esprit d’équipe : il faut encourager la collaboration entre les différents services, niveaux hiérarchiques et fonctions de l’entreprise. Il faut aussi favoriser la participation active de tous les employés dans la recherche d’améliorations.
- L’apprentissage continu : il faut promouvoir la formation continue du personnel, le partage des connaissances et des expériences, et la remise en question permanente des pratiques. Il faut aussi accepter l’échec comme une opportunité d’apprendre et de progresser.
- L’amélioration continue : il faut intégrer la méthode Kaizen comme une partie intégrante du fonctionnement quotidien de l’entreprise. Il faut aussi fixer des objectifs ambitieux mais réalistes, et célébrer chaque amélioration réalisée.
Exemples concrets d’application du Kaizen dans l’industrie
Exemple d’application dans l’industrie automobile
L’un des exemples les plus célèbres d’application du Kaizen dans l’industrie est celui de Toyota. Le constructeur automobile japonais a développé son propre système de production basé sur la méthode Kaizen, appelé le Toyota Production System (TPS). Ce système vise à éliminer les gaspillages, à réduire les coûts, à augmenter la qualité et à satisfaire le client. Le TPS repose sur des principes tels que :
- Le juste-à-temps : il s’agit de produire ce qui est nécessaire, quand c’est nécessaire et en quantité nécessaire, en évitant les stocks inutiles et les surproductions.
- L’autonomation : il s’agit de donner aux machines la capacité de détecter et de signaler les anomalies, en arrêtant le processus si nécessaire, afin d’éviter la propagation des défauts.
- Le kaizen : il s’agit d’impliquer tous les employés dans la recherche permanente d’améliorations, en utilisant des outils tels que le PDCA, le 5S, le Kanban, etc.
Grâce au TPS, Toyota est devenu l’un des leaders mondiaux de l’industrie automobile, en termes de qualité, de productivité et de rentabilité.
Exemple d’application dans l’industrie technologique
Un autre exemple d’application du Kaizen dans l’industrie est celui de Intel. Le géant américain des semi-conducteurs a adopté la méthode Kaizen pour améliorer ses processus de fabrication et de conception. Intel utilise notamment des outils tels que :
- Le Six Sigma : il s’agit d’une méthode qui vise à réduire la variabilité et les défauts dans les processus, en utilisant des outils statistiques et des équipes projet.
- Le Design for Six Sigma (DFSS) : il s’agit d’une méthode qui vise à intégrer les principes du Six Sigma dès la phase de conception des produits ou des services, en utilisant des outils tels que le QFD (Quality Function Deployment) ou le TRIZ (Theory of Inventive Problem Solving).
- Le Lean Six Sigma : il s’agit d’une méthode qui combine les principes du lean management et du Six Sigma, en visant à éliminer les gaspillages et à réduire la variabilité dans les processus.
Grâce au Kaizen, Intel a pu améliorer sa qualité, sa fiabilité, sa compétitivité et sa capacité d’innovation.
Conclusion: L’impact à long terme de Kaizen dans l’industrie
Avantages compétitifs d’une stratégie continuelle d’amélioration
La méthode Kaizen offre aux entreprises industrielles des avantages compétitifs durables. En effet, en adoptant une stratégie continuelle d’amélioration, les entreprises industrielles peuvent :
- S’adapter aux changements du marché : en étant à l’écoute des besoins et des attentes des clients, en anticipant les tendances et les opportunités, en innovant et en améliorant constamment leurs produits et leurs services.
- Se différencier de la concurrence : en offrant une valeur supérieure au client, en proposant des solutions personnalisées et adaptées, en créant une relation de confiance et de fidélité.
- Se développer durablement : en optimisant l’utilisation des ressources, en réduisant l’impact environnemental, en respectant les normes et les réglementations, en contribuant au bien-être social.
Le rôle du Kaizen dans l’évolution et l’avenir de l’industrie
La méthode Kaizen joue également un rôle important dans l’évolution et l’avenir de l’industrie. En effet, en adoptant la méthode Kaizen, les entreprises industrielles peuvent :
- Faire face aux défis actuels : la mondialisation, la digitalisation, la robotisation, la transition énergétique, la crise sanitaire, etc.
- Anticiper les opportunités futures : les nouvelles technologies, les nouveaux marchés, les nouveaux besoins, les nouvelles attentes, etc.
- Créer un avantage compétitif durable : la qualité, la productivité, la rentabilité, la satisfaction client, la motivation employé, etc.
La méthode Kaizen est donc une méthode qui permet aux entreprises industrielles de s’adapter, de se différencier et de se développer dans un environnement complexe et incertain.
En conclusion, la méthode Kaizen est une méthode qui vise à améliorer continuellement les processus et les systèmes dans les entreprises industrielles. Elle repose sur des principes simples mais efficaces, qui impliquent tous les acteurs de l’entreprise. Elle offre des avantages compétitifs durables et permet de faire face aux défis actuels et futurs. La méthode Kaizen est donc une méthode clé pour l’industrie.