Comprendre les 7 mudas.
Dans le monde de l’industrie, la compétitivité est un enjeu majeur. Pour optimiser la production, réduire les coûts et satisfaire les clients, il est essentiel de limiter les gaspillages dans les processus. C’est ce que propose le lean management, une méthode d’amélioration continue inspirée du système de production Toyota. Le lean management repose sur la notion de muda, un terme japonais qui signifie « futilité », « inutilité » ou « gaspillage ».
Mais qu’est-ce qu’un muda exactement ? Quels sont les différents types ? Comment les identifier et les éliminer ? C’est ce que nous allons voir dans cet article.
Présentation des 7 mudas
Qu’est-ce que Muda?
Un muda est une activité qui consomme des ressources (matières premières, temps, énergie, etc.) sans créer de valeur ajoutée pour le client. Autrement dit, c’est une action qui n’apporte rien au produit ou au service final, mais qui génère des coûts et des délais supplémentaires. Par exemple, stocker des produits finis en attente de livraison est un muda, car cela immobilise du capital et de l’espace sans augmenter la qualité du produit.
Origine et contexte de la notion de Muda
La notion de muda a été développée par Taiichi Ohno, l’un des pères fondateurs du système de production Toyota (TPS). Le TPS est un modèle d’organisation industrielle basé sur la philosophie lean, qui vise à éliminer tout ce qui n’apporte pas de valeur au client. Le TPS repose sur trois principes fondamentaux : le juste-à-temps (JIT), qui consiste à produire ce dont le client a besoin, quand il en a besoin et en quantité suffisante ; le jidoka, qui consiste à arrêter le processus en cas de problème et à résoudre la cause à la source ; et le kaizen, qui consiste à impliquer tous les acteurs dans une démarche d’amélioration continue.
Pour mettre en œuvre ces principes, Taiichi Ohno a identifié sept types de gaspillages (mudas) à éliminer dans le processus de production. Il a également défini deux autres concepts liés : le mura désigne l’irrégularité ou la variabilité dans le processus, qui entraîne des fluctuations de la demande, des ruptures de stock ou des surcharges de travail. Le muri désigne la surcharge ou l’excès dans le processus, qui sollicite trop les machines ou les opérateurs, au-delà de leurs capacités. Le mura et le muri sont souvent à l’origine des mudas, et doivent donc être également réduits.
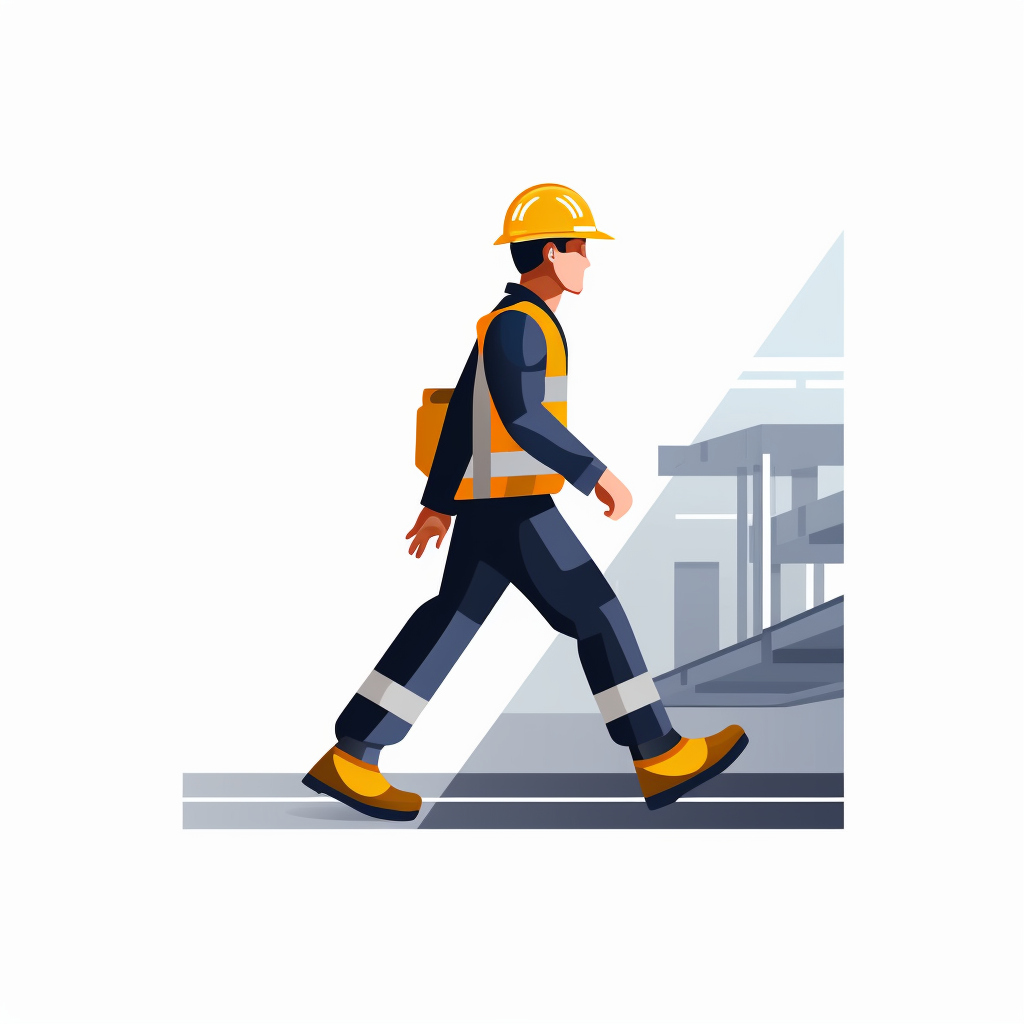
Le détail des 7 mudas dans le processus de production
Muda de surproduction
Le muda de surproduction est le fait de produire plus que ce que le client demande ou plus tôt que nécessaire. C’est l’un des pires, car il entraîne tous les autres. En effet, produire trop ou trop tôt implique d’utiliser plus de matières premières, d’énergie, de main-d’œuvre et d’équipements que nécessaire. Cela génère également plus de stocks, plus de transports, plus d’attentes et plus de risques de défauts. La surproduction peut être causée par une mauvaise prévision de la demande, une mauvaise planification de la production ou une peur du manque.
Muda d’attente
Le muda d’attente est le fait d’avoir des temps morts dans le processus, où les machines ou les opérateurs sont inactifs. Cela représente une perte de productivité et un allongement des délais. Les causes sont souvent des pannes, des ruptures de stock, des changements d’outils, des contrôles qualité ou des problèmes de coordination. Il peut être réduit en optimisant le flux de production, en réduisant les temps de changement de série ou en utilisant des systèmes d’alerte.
Muda de transport
Le muda de transport est le fait de déplacer les produits ou les matières premières d’un point à un autre sans ajouter de valeur. Cela représente un coût supplémentaire, une perte de temps et un risque d’endommagement ou de perte. Ce gaspillage peut être causé par une mauvaise disposition des machines, des distances trop importantes entre les postes de travail ou des flux mal organisés. Il peut être réduit en rapprochant les opérations, en simplifiant les circuits ou en utilisant des moyens de transport adaptés.
Muda de stockage excessif
Le muda de stockage excessif est le fait d’avoir des quantités trop importantes de produits finis, de produits en cours ou de matières premières. Cela représente un coût financier, un coût d’espace et un coût d’entretien. De plus, les stocks peuvent se dégrader, se périmer ou se démoder avec le temps. Le stockage excessif peut être causé par une surproduction, une mauvaise gestion des approvisionnements ou une faible rotation des produits. Il peut être réduit en adoptant le principe du juste-à-temps, en synchronisant la production avec la demande ou en utilisant des systèmes de gestion des stocks comme le kanban.
Muda de processus inutiles
Le muda de processus inutiles est le fait d’effectuer des opérations qui n’apportent pas de valeur au produit ou qui ne sont pas demandées par le client. Cela représente un gaspillage de ressources et une perte de qualité. Par exemple, appliquer un traitement supplémentaire à un produit qui ne le nécessite pas ou réaliser un contrôle qualité trop fréquent sont des mudas de processus inutiles. Il peut être causé par un manque de connaissance des besoins du client, par une mauvaise conception du produit ou par une habitude non remise en question. Il peut être réduit en analysant la valeur ajoutée de chaque opération, en simplifiant le processus ou en utilisant des outils comme la méthode des 5S.
Muda de mouvements excessifs
Le muda de mouvements excessifs est le fait d’effectuer des gestes inutiles ou inefficaces lors du travail. Cela représente une perte de temps, une fatigue accrue et un risque d’accident. Par exemple, se déplacer fréquemment pour chercher un outil, se pencher ou se tourner pour atteindre une pièce ou manipuler plusieurs fois le même objet sont des mudas de mouvements excessifs. Ce type peut être causé par une mauvaise organisation du poste de travail, par un manque d’ergonomie ou par une absence d’instructions claires. Il peut être réduit en améliorant l’agencement du poste, en adaptant les équipements aux opérateurs ou en standardisant les gestes.
Muda de défauts de production
Le muda de défauts de production est le fait de produire des pièces non conformes aux spécifications du client ou aux normes internes. Cela représente un coût direct, lié à la réparation ou au remplacement des pièces défectueuses, et un coût indirect, lié à la perte de confiance du client, à la détérioration de l’image de marque ou à la baisse du chiffre d’affaires. Le muda de défauts peut être causé par une mauvaise qualité des matières premières, par un réglage incorrect des machines, par une erreur humaine ou par un manque de contrôle. Il peut être réduit en renforçant la qualité à la source, en appliquant le principe du jidoka ou en utilisant des outils comme le diagramme d’Ishikawa.
Comprendre et identifier les mudas
Comment détecter un muda dans son entreprise ?
Pour détecter un muda dans son entreprise, il faut se poser les bonnes questions. Quelle est la valeur ajoutée de chaque activité ? Quelles sont les attentes du client ? Quels sont les coûts et les délais associés à chaque activité ? Quels sont les risques et les opportunités d’amélioration ? Pour répondre à ces questions, il existe plusieurs méthodes et outils, tels que :
- L’analyse de la chaîne de valeur (VSM), qui consiste à cartographier les flux de matières et d’informations entre les différentes étapes du processus, en identifiant les temps, les coûts, les stocks et les sources de gaspillage.
- L’observation directe du terrain (gemba), qui consiste à se rendre sur le lieu où se déroule le travail, pour voir la réalité des opérations, écouter les problèmes des opérateurs et recueillir des données factuelles.
- La méthode des 5 pourquoi, qui consiste à remonter à la cause racine d’un problème en se posant cinq fois la question « pourquoi ? », jusqu’à ce qu’on trouve la véritable origine du muda.
Les conséquences d’un muda sur l’entreprise
Un muda a des conséquences négatives sur l’entreprise, à plusieurs niveaux. Sur le plan financier, il représente un coût inutile, qui réduit la rentabilité de l’entreprise. Sur le plan opérationnel, un muda entraîne une baisse de la productivité, une augmentation des délais et une diminution de la flexibilité. Sur le plan humain, cela engendre une perte de motivation, une frustration et un stress pour les opérateurs. Sur le plan stratégique, un muda affecte la satisfaction et la fidélisation des clients, ainsi que la compétitivité et la pérennité de l’entreprise.
L’élimination des mudas
Les stratégies d’élimination des mudas
Pour les éliminer, il faut adopter une démarche systématique et participative, qui implique tous les acteurs de l’entreprise. Il existe plusieurs stratégies possibles, selon le type de muda et le contexte. Parmi ces stratégies, on peut citer :
- La standardisation des processus, qui consiste à définir et à appliquer des règles claires et précises pour chaque activité, afin d’éviter les variations, les erreurs et les répétitions.
- L’amélioration continue (kaizen), qui consiste à rechercher en permanence des opportunités d’amélioration, en impliquant les opérateurs dans la résolution des problèmes et la proposition d’idées.
- L’innovation radicale (kaikaku), qui consiste à remettre en cause le processus existant et à proposer des solutions novatrices, qui permettent de réaliser un saut qualitatif ou quantitatif.
- La simplification du produit (poka-yoke), qui consiste à concevoir le produit de manière à éviter ou à détecter les erreurs lors de sa fabrication ou de son utilisation.
- La conception du processus (QFD), qui consiste à partir des besoins du client pour définir les caractéristiques du produit et les exigences du processus.
Cas d’application concrets dans l’industrie
De nombreuses entreprises ont réussi à éliminer les mudas dans leurs processus de production, en appliquant les principes du lean management. Voici quelques exemples concrets :
- Toyota a réduit ses coûts de production de 30 % en éliminant les mudas de surproduction, d’attente et de transport, grâce au système kanban, qui permet de synchroniser la production avec la demande.
- General Electric a augmenté sa productivité de 40 % en éliminant les mudas de stockage excessif et de processus inutiles, grâce à la méthode Six Sigma, qui vise à réduire la variabilité et à améliorer la qualité.
- Nike a réduit ses déchets de 19 % en éliminant les mudas de mouvements excessifs et de défauts de production, grâce à la technologie Flyknit, qui permet de fabriquer des chaussures sans couture ni découpe.
Les bénéfices attendus de l’élimination des mudas
L’élimination des mudas apporte de nombreux bénéfices à l’entreprise, à court et à long terme. Parmi ces bénéfices, on peut citer :
- Une réduction des coûts de production, grâce à une meilleure utilisation des ressources.
- Une augmentation de la qualité des produits ou services, grâce à une réduction des défauts et des retours.
- Une amélioration de la satisfaction et de la fidélité des clients, grâce à une meilleure réponse à leurs besoins et à leurs attentes.
- Une optimisation de la performance opérationnelle, grâce à une réduction des délais et à une augmentation de la flexibilité.
- Une amélioration du climat social, grâce à une valorisation du travail et à une implication des opérateurs.
- Une consolidation de l’avantage concurrentiel, grâce à une différenciation par la valeur ajoutée et par l’innovation.
Conclusion : les mudas, un outil de performance continu
Les mudas sont des gaspillages qui affectent la performance de l’entreprise. Ils sont présents dans tous les processus de production, quels que soient le secteur d’activité ou la taille de l’entreprise. Pour les éliminer, il faut adopter une démarche lean, qui vise à créer de la valeur pour le client en réduisant les sources de non-valeur. Leur élimination permet d’améliorer la qualité, la productivité, la rentabilité et la compétitivité de l’entreprise. C’est un outil de performance continu, qui nécessite une remise en question permanente et une participation active de tous les acteurs.
Pour aller plus loin dans l’élimination des mudas, nous vous recommandons de consulter le reste du site Shizen, qui propose une solution innovante pour optimiser vos processus industriels. Shizen est un partenaire idéal pour vous accompagner dans votre démarche lean et vous faire gagner en performance.