L’andon est un outil de management visuel qui permet de signaler et de résoudre les problèmes survenant dans un processus de production. Il fait partie des outils lean management, une méthode d’amélioration continue inspirée du Toyota Production System.
Mais comment l’utiliser efficacement ? Quels sont ses avantages et ses limites ? Quels sont les exemples d’application de l’andon dans différentes industries ? Cet article vous donne toutes les réponses pour maîtriser cet outil indispensable à la performance industrielle.
Comprendre l’Andon
Définition et origines de l’Andon
L’andon est un terme japonais qui signifie « lanterne » ou « lumière« . Il désigne un système d’alerte visuelle qui indique l’état d’un processus de production à l’aide de colonnes lumineuses, de tableaux de bord ou d’écrans. Il permet aux opérateurs de signaler un problème (arrêt machine, défaut qualité, rupture de stock, etc.) en actionnant un bouton ou en tirant sur un cordon. Le problème est alors visible par tous les acteurs du processus, y compris le team leader, le responsable de production ou le service maintenance. L’objectif est de réagir rapidement pour résoudre le problème et éviter qu’il ne se propage ou qu’il ne se reproduise.
L’andon est né dans les années 1950 au sein du Toyota Production System (TPS), le système de production qui a fait la renommée du constructeur automobile japonais. Le TPS repose sur deux principes fondamentaux : le juste-à-temps (JIT) et le jidoka. Le JIT vise à réduire les gaspillages en produisant uniquement ce qui est nécessaire, quand c’est nécessaire et en quantité nécessaire. Le jidoka vise à garantir la qualité en arrêtant le processus dès qu’un problème est détecté, afin d’éviter de produire des pièces défectueuses.
C’est un outil qui permet de mettre en œuvre le jidoka, en donnant aux opérateurs le pouvoir d’arrêter la chaîne de production en cas d’anomalie.
L’andon dans le système Lean
L’andon fait partie des outils lean management, une méthode d’amélioration continue qui vise à optimiser la performance des processus en éliminant les gaspillages et en maximisant la valeur ajoutée pour le client. Le lean management s’inspire du TPS et s’applique à tous les secteurs d’activité, pas seulement à l’industrie automobile. Le lean management repose sur la participation active des opérateurs, qui sont considérés comme les experts de leur poste de travail et les acteurs principaux du changement.
Le lean management utilise des outils visuels pour faciliter la communication, la coordination et la résolution des problèmes. L’andon est l’un de ces outils visuels, qui permet de rendre visible les problèmes et de solliciter l’aide des personnes compétentes pour les résoudre.
Principe de fonctionnement de l’Andon
Cas d’utilisation de l’Andon dans une production
Pour illustrer son principe de fonctionnement, prenons l’exemple d’une ligne de production composée de plusieurs postes de travail. Chaque poste dispose d’un bouton ou d’un cordon andon, relié à une colonne lumineuse située au-dessus du poste. La colonne lumineuse peut afficher différentes couleurs selon l’état du poste : vert (normal), jaune (alerte), rouge (arrêt), bleu (maintenance). La colonne lumineuse est également reliée à un tableau de bord central, qui affiche le numéro du poste ayant déclenché l’alerte, ainsi que le type et la durée du problème.
Imaginons qu’un opérateur détecte un défaut sur une pièce qu’il vient de produire. Il appuie alors sur le bouton andon, ce qui allume la colonne lumineuse en rouge et arrête la ligne de production. Le tableau de bord central affiche le numéro du poste, le type de problème (qualité) et le temps écoulé depuis l’alerte. Le team leader, qui supervise la ligne de production, se rend immédiatement au poste concerné pour identifier la cause du défaut et aider l’opérateur à le résoudre.
Si le problème est résolu rapidement, l’opérateur appuie à nouveau sur le bouton andon, ce qui éteint la colonne lumineuse et relance la ligne de production. Si le problème nécessite l’intervention du service maintenance, l’opérateur appuie sur un autre bouton, ce qui allume la colonne lumineuse en bleu et envoie une notification au service maintenance. Le service maintenance se rend alors au poste concerné pour effectuer la réparation. Une fois le problème résolu, le service maintenance appuie sur le bouton, ce qui éteint la colonne lumineuse et relance la ligne de production.
Les différents types d’Andons
Il existe différents types d’andons, selon le mode de déclenchement de l’alerte, le type de signal visuel utilisé et le niveau d’information fourni. On peut distinguer les types suivants :
- manuel : l’alerte est déclenchée par l’opérateur qui appuie sur un bouton ou tire sur un cordon. Le signal visuel est généralement une colonne lumineuse qui change de couleur selon l’état du poste. L’information fournie est limitée au numéro du poste et au type de problème.
- automatique : l’alerte est déclenchée automatiquement par un capteur qui détecte une anomalie dans le processus (par exemple, une variation de température, de pression, de vitesse, etc.). Le signal visuel peut être une colonne lumineuse, mais aussi un écran qui affiche des données chiffrées ou graphiques. L’information fournie est plus détaillée et permet d’identifier la cause du problème.
- sonore : l’alerte est accompagnée d’un signal sonore (par exemple, une sirène, une cloche, une voix) qui attire l’attention des acteurs du processus. Le signal sonore peut être modulé selon la nature et l’urgence du problème. L’andon sonore peut être combiné avec un andon visuel pour renforcer l’efficacité du système.
- numérique : l’alerte est transmise par un système informatique qui envoie des notifications aux personnes concernées (par exemple, par SMS, par e-mail, par application mobile). Le signal numérique permet de communiquer avec des personnes qui ne sont pas présentes sur le lieu de production (par exemple, le responsable qualité, le fournisseur, le client). L’andon numérique peut être combiné avec un andon visuel pour assurer un suivi en temps réel du processus.
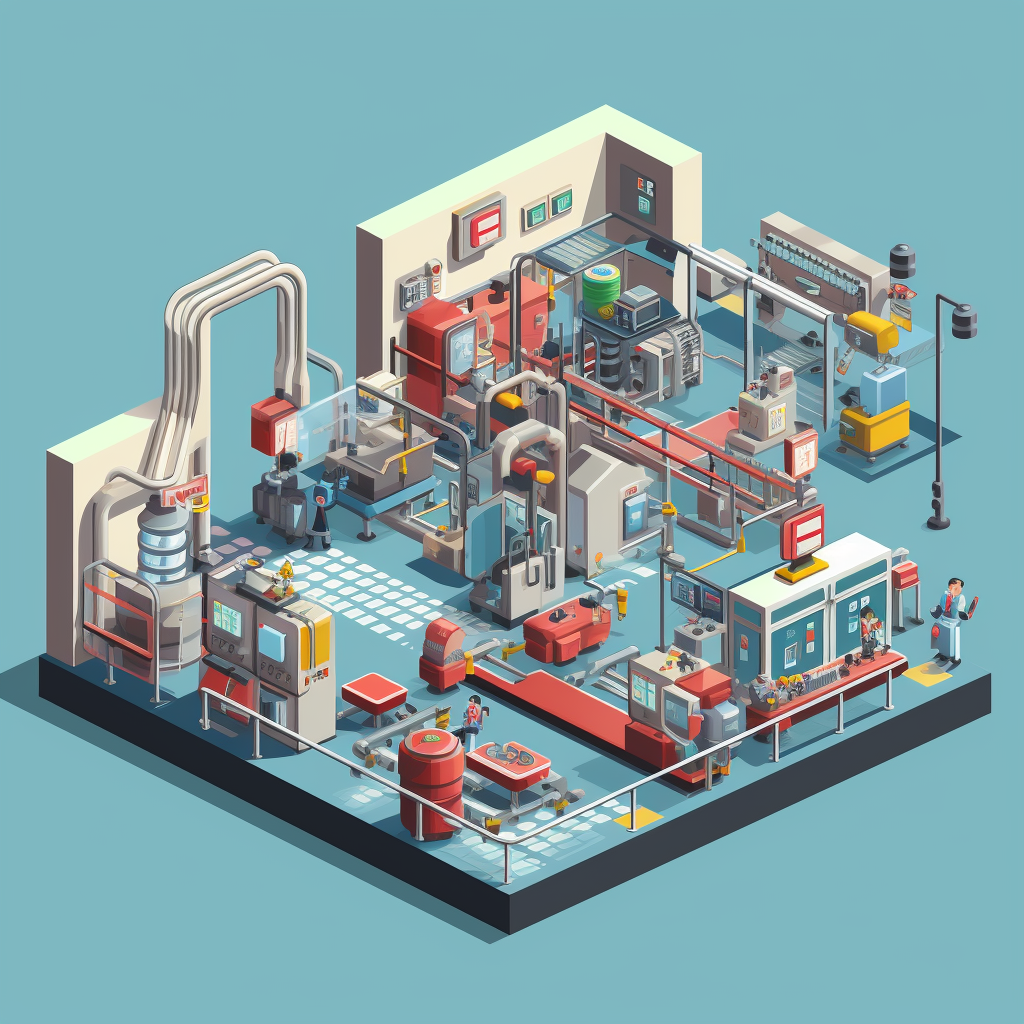
Comment utiliser l’Andon efficacement ?
Identifier les opportunités pour l’Andon
L’utilisation de l’andon n’est pas pertinente pour tous les processus de production. Il faut donc identifier les opportunités en fonction des caractéristiques du processus et des objectifs visés. Voici quelques critères à prendre en compte pour déterminer si son utilisation est adaptée à votre processus :
- La complexité du processus : plus le processus est complexe, plus il est susceptible de générer des problèmes. L’utilisation de l’andon peut alors être utile pour simplifier la communication et la coordination entre les acteurs du processus.
- La fréquence des problèmes : plus le processus est sujet à des problèmes fréquents ou récurrents, plus il est nécessaire de les signaler et de les résoudre rapidement. L’utilisation de l’andon peut alors être efficace pour réduire les temps d’arrêt et les coûts associés.
- La criticité des problèmes : plus les problèmes ont un impact négatif sur la qualité du produit ou sur la satisfaction du client, plus il est important de les prévenir ou de les corriger immédiatement. L’utilisation de l’andon peut alors être bénéfique pour améliorer la qualité du produit et la satisfaction du client.
- La variabilité du processus : plus le processus est soumis à des variations internes ou externes (par exemple, des changements de demande, de matière première, de personnel, etc.), plus il est difficile de le contrôler et de le stabiliser. On peut alors l’utiliser pour détecter les écarts et les ajuster rapidement.
- La standardisation du processus : plus le processus est standardisé, c’est-à-dire qu’il suit des règles et des procédures claires et précises, plus il est facile de définir les conditions normales et anormales du processus. On peut alors l’utiliser pour respecter les standards de travail et les améliorer en continu.
Astuces pour une mise en œuvre réussie de l’Andon
Une fois que vous avez identifié les opportunités, il faut mettre en place le système d’alerte visuelle qui convient le mieux à votre processus. Voici quelques astuces pour une mise en œuvre réussie :
- Choisir le type adapté à votre processus : selon le mode de déclenchement de l’alerte, le type de signal visuel utilisé et le niveau d’information fourni, vous pouvez opter pour un andon manuel, automatique, sonore ou numérique. Vous pouvez également combiner plusieurs types pour renforcer l’efficacité du système.
- Choisir les couleurs et les sons appropriés pour l’andon : selon la nature et l’urgence du problème, vous pouvez utiliser différentes couleurs et différents sons pour attirer l’attention des acteurs du processus. Par exemple, vous pouvez utiliser le rouge pour indiquer un arrêt du processus, le jaune pour indiquer une alerte, le vert pour indiquer un fonctionnement normal, le bleu pour indiquer une demande de maintenance. Vous pouvez également utiliser des sons modulés selon la fréquence ou l’intensité pour indiquer le niveau de gravité du problème.
- Choisir l’emplacement optimal : selon la taille et la configuration du lieu de production, vous pouvez le placer au-dessus du poste de travail, sur un mur ou sur un écran. L’important est qu’il soit visible par tous les acteurs du processus, y compris le team leader, le responsable de production ou le service maintenance. Vous pouvez également utiliser des miroirs ou des caméras pour augmenter la visibilité de l’andon.
- Former les opérateurs à l’utilisation de l’andon : il est essentiel que les opérateurs soient formés, afin qu’ils comprennent son fonctionnement, son intérêt et ses règles. Il faut leur expliquer comment déclencher l’alerte, comment interpréter les signaux visuels et sonores, comment réagir face au problème et comment confirmer sa résolution. Il faut également leur faire comprendre que l’utilisation de l’andon n’est pas une sanction, mais une opportunité d’amélioration.
- Suivre et analyser les données : il est important de collecter et d’analyser les données issues de l’andon, afin d’évaluer son efficacité, d’identifier les causes racines des problèmes et de mettre en place des actions correctives ou préventives. Vous pouvez utiliser des indicateurs tels que le nombre d’alertes déclenchées, la durée moyenne des arrêts, le taux de résolution des problèmes, etc. Vous pouvez également utiliser des outils tels que le diagramme d’Ishikawa ou le 5 pourquoi pour analyser les causes des problèmes.
Avantages et limites de l’utilisation de l’Andon
Les avantages de l’utilisation de l’Andon
L’utilisation de l’andon présente de nombreux avantages pour la performance industrielle. Voici quelques-uns des principaux bénéfices que vous pouvez obtenir :
- Améliorer la qualité du produit : en signalant et en résolvant rapidement les problèmes liés à la qualité, vous évitez de produire des pièces défectueuses, de gaspiller des matières premières ou de livrer des produits non conformes. Vous réduisez ainsi les coûts de non-qualité et vous augmentez la satisfaction du client.
- Améliorer la productivité du processus : en signalant et en résolvant rapidement les problèmes liés au processus, vous évitez les temps d’arrêt, les pertes de cadence ou les retards de livraison. Vous optimisez ainsi l’utilisation des ressources et vous augmentez la capacité de production.
- Améliorer la sécurité du personnel : en signalant et en résolvant rapidement les problèmes liés à la sécurité, vous évitez les accidents, les blessures ou les maladies professionnelles. Vous protégez ainsi la santé et le bien-être de vos collaborateurs et vous réduisez les coûts liés aux arrêts de travail ou aux indemnisations.
- Améliorer la communication et la collaboration entre les acteurs du processus : en rendant visible les problèmes et en sollicitant l’aide des personnes compétentes, vous favorisez le partage d’information, le dialogue et l’entraide entre les opérateurs, le team leader, le responsable de production ou le service maintenance. Vous créez ainsi une culture d’amélioration continue et vous renforcez l’engagement de vos équipes.
Les défis et les limites de l’Andon
L’utilisation de l’andon n’est pas sans difficultés ni inconvénients. Voici quelques-uns des principaux défis et limites que vous pouvez rencontrer :
- Choisir le bon niveau d’arrêt du processus : il n’est pas toujours évident de définir quand il faut arrêter le processus en cas de problème. Si vous arrêtez trop souvent le processus, vous risquez de perturber le flux de production et de réduire la productivité. Si vous n’arrêtez pas assez souvent le processus, vous risquez de laisser passer des problèmes qui peuvent s’aggraver ou se propager. Il faut donc trouver le bon équilibre entre la qualité et la productivité, en fonction des critères de performance définis pour votre processus.
- Gérer la résistance au changement : il n’est pas facile d’impliquer les opérateurs dans l’utilisation de l’andon, car ils peuvent avoir peur d’être jugés, sanctionnés ou stigmatisés pour avoir déclenché une alerte. Il faut donc les rassurer, les encourager et les féliciter pour leur participation à l’amélioration du processus. Il faut également impliquer le management dans le soutien et le suivi de l’utilisation.
- Maintenir l’efficacité du système : il n’est pas suffisant d’installer un système d’andon, il faut également le maintenir en bon état de fonctionnement, le vérifier régulièrement et le faire évoluer en fonction des besoins du processus. Il faut également s’assurer que les données sont exploitées correctement, que les problèmes sont résolus durablement et que les actions d’amélioration sont mises en œuvre.
Exemples d’application de l’Andon dans différentes industries
Etudes de cas d’utilisation de l’Andon
L’andon est utilisé dans de nombreuses industries, que ce soit dans le secteur manufacturier, le secteur des services ou le secteur public. Voici quelques exemples d’application dans différentes industries :
- Dans l’industrie automobile, l’andon est utilisé pour signaler et résoudre les problèmes liés à la qualité, à la sécurité ou à la disponibilité des machines ou des pièces. Par exemple, chez Toyota, chaque opérateur dispose d’un cordon andon qui lui permet d’arrêter la ligne de production en cas d’anomalie. Le problème est alors affiché sur un tableau électronique qui indique sa localisation, sa nature et sa durée. Le team leader se rend alors sur place pour aider l’opérateur à résoudre le problème. Si le problème n’est pas résolu dans un délai imparti, une alarme sonore se déclenche pour alerter le responsable de production ou le service maintenance. L’andon permet ainsi de garantir la qualité du produit et d’améliorer la productivité du processus.
Regards sur l’avenir de l’Andon dans l’industrie 4.0
L’andon est un outil qui évolue avec les technologies et les besoins de l’industrie. Avec l’avènement de l’industrie 4.0, qui repose sur la digitalisation, l’automatisation et l’intelligence artificielle, l’andon devient plus intelligent, plus connecté et plus interactif. Voici quelques exemples de tendances qui marquent son évolution dans l’industrie 4.0 :
- Connecté : grâce aux technologies sans fil (Wi-Fi, Bluetooth, NFC), il peut se connecter à d’autres systèmes informatiques (ERP, MES, CRM) ou à d’autres objets connectés (capteurs, robots, drones) pour collecter et transmettre des données en temps réel. L’andon connecté permet ainsi d’optimiser la gestion des flux, des stocks et des ressources. Sur Shizen par exemple, on peut le connecter via l’API ouverte.
- Intelligent : grâce aux technologies d’intelligence artificielle (machine learning, deep learning, computer vision), il peut analyser les données collectées, détecter les anomalies, prédire les pannes ou les dysfonctionnements, et proposer des solutions optimales. Il peut donc être utilisé afin de prévenir les problèmes, d’améliorer la qualité et de réduire les coûts.
- Interactif : grâce aux technologies d’interface homme-machine (écrans tactiles, réalité augmentée, réalité virtuelle), il peut offrir une expérience utilisateur plus intuitive, plus immersive et plus personnalisée. L’andon interactif permet ainsi de faciliter la communication, la collaboration et la formation des acteurs du processus.
Conclusion
Récapitulatif et clés pour un usage efficace de l’Andon
Pour conclure, l’andon est un outil de management visuel qui permet de signaler et de résoudre les problèmes survenant dans un processus de production. Il fait partie des outils lean management, une méthode d’amélioration continue qui vise à optimiser la performance des processus en éliminant les gaspillages et en maximisant la valeur ajoutée pour le client.
Son utilisation présente de nombreux avantages pour la performance industrielle, mais elle implique également des défis et des limites qu’il faut savoir gérer. Il est utilisé dans de nombreuses industries, que ce soit dans le secteur manufacturier, le secteur des services ou le secteur public. Il évolue avec les technologies et les besoins de l’industrie, et devient plus intelligent, plus connecté et plus interactif.
Pour utiliser l’andon efficacement, voici quelques clés à retenir :
- Identifier les opportunités pour l’andon en fonction des caractéristiques du processus et des objectifs visés.
- Choisir le type adapté à votre processus, en fonction du mode de déclenchement de l’alerte, du type de signal visuel utilisé et du niveau d’information fourni.
- Choisir les couleurs et les sons appropriés, en fonction de la nature et de l’urgence du problème.
- Choisir l’emplacement optimal, en fonction de la taille et de la configuration du lieu de production.
- Former les opérateurs à l’utilisation, en leur expliquant son fonctionnement, son intérêt et ses règles.
- Suivre et analyser les données, en utilisant des indicateurs et des outils appropriés.
Nous espérons que cet article vous a permis de mieux comprendre l’andon, et comment l’utiliser. Si vous avez des questions ou des commentaires, n’hésitez pas à nous contacter.