Introduction au diagramme Yamazumi
Vous devez connaître le diagramme Yamazumi, un outil indispensable pour l’analyse et l’équilibrage des charges de travail dans vos processus de fabrication. Le diagramme Yamazumi vous permet de visualiser le temps consacré à chaque tâche, de distinguer les activités à valeur ajoutée des activités sans valeur ajoutée, et d’identifier les sources de gaspillage et d’amélioration.
Dans cet article, nous allons vous expliquer ce qu’est le diagramme Yamazumi, comment il fonctionne, comment le créer, comment l’utiliser pour optimiser votre production industrielle, et quels sont ses avantages et ses limites. Nous allons également vous présenter des exemples et des études de cas d’application du diagramme Yamazumi dans différents secteurs d’activité.
Définition du diagramme Yamazumi
Le mot Yamazumi signifie “empiler” en japonais. Un diagramme Yamazumi est un graphique à barres empilées qui représente le temps consacré à chaque tâche dans une étape d’un processus. C’est un outil qui permet de visualiser le temps de cycle des machines et des opérateurs, et d’évaluer leur performance. C’est aussi un bon indicateur de la variation entre les postes de travail qui effectuent la même chose. Les variations, ou mura en japonais, entraînent du muda ou du gaspillage sous forme de retards et de stocks excédentaires.
Origine et importance dans le lean manufacturing
Le diagramme Yamazumi a été utilisé dès les années 1950 par les entreprises japonaises de fabrication automobile, comme Toyota, pour leurs activités d’équilibrage des lignes et d’optimisation des flux de travail. Le diagramme Yamazumi fait partie des outils du lean manufacturing, une approche qui vise à éliminer les gaspillages et à maximiser la valeur ajoutée pour le client. Le lean manufacturing repose sur le concept de takt time, qui est le rythme auquel un produit doit être fabriqué pour répondre à la demande du client. Le diagramme Yamazumi permet de comparer le temps de cycle des opérations avec le takt time, et de détecter les écarts qui peuvent nuire à la performance du processus.
Comprendre le fonctionnement du diagramme Yamazumi
Structure et éléments principaux du diagramme
Un diagramme Yamazumi se présente sous la forme d’un graphique à barres empilées, où l’axe des abscisses représente les postes de travail ou les opérateurs, et l’axe des ordonnées représente le temps de cycle par poste ou par opérateur. Chaque bloc dans une pile représente une tâche dans ce poste ou par cet opérateur.
Les tâches sont généralement codées par couleur pour indiquer si elles sont à valeur ajoutée ou sans valeur ajoutée. Une tâche est considérée comme à valeur ajoutée si elle transforme le produit ou le service en quelque chose que le client est prêt à payer. Une tâche est considérée comme sans valeur ajoutée si elle n’apporte rien au client ou si elle peut être évitée. Les tâches sans valeur ajoutée sont souvent divisées en deux catégories : les tâches nécessaires, qui sont requises par le système ou l’entreprise, et les tâches inutiles, qui sont purement du gaspillage.
Les diagrammes Yamazumi comportent généralement le takt time mis en évidence horizontalement dans le graphique. Tout poste, opérateur ou temps de processus qui dépasse le takt time est immédiatement candidat à l’optimisation. En un coup d’œil, on peut savoir combien de temps une tâche prend dans le processus. C’est un outil simple mais puissant qui permet de localiser où les problèmes se produisent.
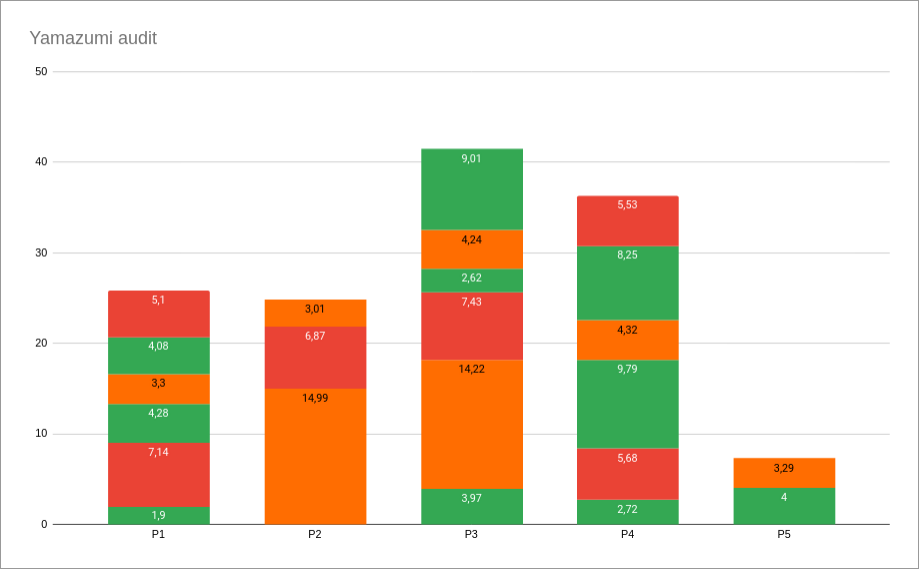
Comment interpréter un diagramme Yamazumi ?
Pour interpréter un diagramme Yamazumi, il faut comparer le temps de cycle des postes ou des opérateurs avec le takt time, et analyser la répartition des tâches à valeur ajoutée et sans valeur ajoutée. Voici quelques règles générales pour interpréter un diagramme Yamazumi :
- Si le temps de cycle d’un poste ou d’un opérateur est inférieur au takt time, cela signifie qu’il y a de la capacité disponible pour effectuer d’autres tâches ou pour aider d’autres postes.
- Si le temps de cycle d’un poste ou d’un opérateur est égal au takt time, cela signifie qu’il est parfaitement aligné sur la demande du client et qu’il n’y a pas de gaspillage de temps.
- Si le temps de cycle d’un poste ou d’un opérateur est supérieur au takt time, cela signifie qu’il y a un goulot d’étranglement qui ralentit le processus et qu’il faut réduire le temps de cycle ou répartir les tâches différemment.
- Si la majorité des tâches sont à valeur ajoutée, cela signifie que le processus est efficace et qu’il crée de la valeur pour le client.
- Si la majorité des tâches sont sans valeur ajoutée, cela signifie que le processus est inefficace et qu’il génère du gaspillage. Il faut alors éliminer les tâches inutiles et minimiser les tâches nécessaires.
En interprétant un diagramme Yamazumi, on peut identifier les opportunités d’amélioration du processus et définir des actions correctives pour optimiser la production industrielle.
Création d’un diagramme Yamazumi
Étapes de préparation pour la création d’un diagramme Yamazumi
Pour créer un diagramme Yamazumi, il faut suivre quelques étapes de préparation :
- Définir l’objectif et le périmètre du diagramme Yamazumi. Il faut savoir pourquoi on veut utiliser cet outil et quel processus on veut analyser.
- Identifier les parties prenantes du projet. Il faut impliquer les personnes qui connaissent bien le processus, comme les opérateurs, les superviseurs, les ingénieurs ou les managers.
- Déterminer le takt time du processus. Il faut calculer le rythme auquel le produit ou le service doit être livré au client en fonction de la demande et du temps disponible.
- Collecter les données sur le temps de cycle des postes ou des opérateurs. Il faut mesurer le temps consacré à chaque tâche dans chaque étape du processus en utilisant des méthodes comme l’observation directe, les chronomètres ou les capteurs.
- Classer les tâches en fonction de leur valeur ajoutée. Il faut distinguer les tâches qui créent de la valeur pour le client des tâches qui n’en créent pas, et identifier les sources de gaspillage.
Choix des opérations et tâches à inclure
Pour choisir les opérations et les tâches à inclure dans le diagramme Yamazumi, il faut se baser sur le périmètre défini lors de la préparation. Il faut inclure toutes les opérations et toutes les tâches qui sont impliquées dans la fabrication du produit ou du service, en tenant compte des contraintes techniques, organisationnelles et réglementaires. Il faut également inclure les tâches de support, comme le contrôle qualité, le nettoyage ou la maintenance. Il faut éviter d’omettre ou de regrouper des tâches qui pourraient fausser l’analyse du temps de cycle. Il faut également veiller à utiliser un niveau de détail cohérent pour toutes les tâches, afin de faciliter la comparaison et l’interprétation.
Comment mesurer et représenter le temps d’une tâche ?
Pour mesurer et représenter le temps d’une tâche, il faut utiliser des unités de temps appropriées, comme les secondes, les minutes ou les heures. Il faut également distinguer le temps opérationnel du temps total. Le temps opérationnel est le temps réellement consacré à la réalisation de la tâche, sans compter les interruptions ou les attentes. Le temps total est le temps écoulé entre le début et la fin de la tâche, en comptant les interruptions ou les attentes.
Le diagramme Yamazumi se base généralement sur le temps opérationnel, car il reflète mieux la performance du processus. Pour représenter le temps d’une tâche dans le diagramme Yamazumi, il faut utiliser une hauteur proportionnelle à la durée de la tâche. Par exemple, si une tâche prend 10 secondes et que l’unité de mesure est la seconde, il faut utiliser une hauteur de 10 unités pour cette tâche.
Utilisation du diagramme Yamazumi pour l’optimisation de la production industrielle
Identification des goulots d’étranglement et des inégalités de travail
Une fois le diagramme Yamazumi créé, il faut l’utiliser pour identifier les goulots d’étranglement et les inégalités de travail dans le processus. Un goulot d’étranglement est un poste ou un opérateur dont le temps de cycle est supérieur au takt time, ce qui crée un déséquilibre dans le flux de production et entraîne des retards et des stocks. Une inégalité de travail est une différence significative entre le temps de cycle des postes ou des opérateurs qui effectuent la même chose, ce qui crée un désalignement entre les capacités disponibles et les besoins du processus.
Pour identifier les goulots d’étranglement et les inégalités de travail, il faut examiner le diagramme Yamazumi et repérer les postes ou les opérateurs dont le temps de cycle dépasse le takt time ou qui présentent une grande variabilité par rapport aux autres. Ces postes ou opérateurs sont les principaux candidats à l’optimisation.
Optimisation de la répartition des tâches
Pour optimiser la répartition des tâches dans le processus, il faut chercher à équilibrer le temps de cycle des postes ou des opérateurs avec le takt time, et à réduire la variabilité entre eux. Pour cela, il existe plusieurs méthodes possibles :
- Réduire le nombre ou la durée des tâches sans valeur ajoutée. Il s’agit d’éliminer ou de minimiser les activités qui n’apportent rien au client ou qui peuvent être évitées, comme les déplacements inutiles, les attentes, les erreurs, les reprises ou les surproductions.
- Déplacer ou partager certaines tâches entre les postes ou les opérateurs. Il s’agit de transférer ou de répartir certaines activités entre les postes ou les opérateurs qui ont de la capacité disponible, afin de soulager ceux qui sont surchargés ou qui créent un goulot d’étranglement.
- Standardiser ou simplifier certaines tâches. Il s’agit d’uniformiser ou de simplifier certaines activités qui présentent une grande variabilité ou une complexité excessive, afin de réduire le temps de cycle et d’améliorer la qualité.
- Former ou qualifier davantage les opérateurs. Il s’agit d’améliorer les compétences ou la polyvalence des opérateurs, afin de réduire le temps de cycle et d’augmenter la flexibilité.
En optimisant la répartition des tâches, on peut réduire les goulots d’étranglement et les inégalités de travail, et améliorer l’équilibrage des lignes de production.
Amélioration du flux de production grâce au diagramme Yamazumi
En améliorant le flux de production grâce au diagramme Yamazumi, on peut obtenir plusieurs bénéfices pour la production industrielle :
- Réduire les coûts de production. En éliminant les gaspillages et en optimisant les ressources, on peut diminuer les coûts liés aux stocks, aux déchets, aux rejets ou aux arrêts.
- Améliorer la qualité des produits ou des services. En réduisant les erreurs et les reprises, on peut augmenter la conformité aux exigences du client et diminuer les retours ou les réclamations.
- Augmenter la productivité et la capacité de production. En réduisant le temps de cycle et en équilibrant les charges de travail, on peut accroître le rendement et la cadence de production, et répondre plus rapidement à la demande.
- Satisfaire et fidéliser les clients. En livrant des produits ou des services de qualité dans les délais, on peut renforcer la confiance et la satisfaction des clients, et créer un avantage concurrentiel.
En utilisant le diagramme Yamazumi pour améliorer le flux de production, on peut donc optimiser la performance globale du processus et créer plus de valeur pour le client.
Exemples et études de cas d’application du diagramme Yamazumi
Utilisation dans l’industrie automobile
L’industrie automobile est l’un des secteurs où le diagramme Yamazumi est le plus utilisé, car il permet d’optimiser les processus de fabrication complexes et variés qui impliquent de nombreuses opérations et tâches. Par exemple, Toyota utilise le diagramme Yamazumi pour équilibrer ses lignes d’assemblage et réduire ses temps de cycle.
En utilisant le diagramme Yamazumi, Toyota a pu identifier les goulots d’étranglement dans ses processus, éliminer les activités sans valeur ajoutée, répartir les tâches entre les opérateurs, standardiser les méthodes de travail, former les employés à la polyvalence, et améliorer la qualité et la productivité. Grâce au diagramme Yamazumi, Toyota a pu atteindre un niveau d’excellence opérationnelle reconnu mondialement.
Toyota Motor Manufacturing France a également choisi d’installer Shizen dans toute son usine, une solution logicielle qui aide les industriels à résoudre 3 fois plus de problèmes, grâce à une structuration des informations et communications. Shizen permet d’optimiser le processus de résolution des problèmes, en facilitant la collecte, l’analyse et le partage des données.
Application dans l’industrie agroalimentaire
L’industrie agroalimentaire est un autre secteur où le diagramme Yamazumi peut être utile, car il permet d’optimiser les processus de fabrication qui doivent respecter des contraintes sanitaires, réglementaires et environnementales. Par exemple, une entreprise agroalimentaire spécialisée dans la fabrication de produits laitiers a utilisé le diagramme Yamazumi pour analyser son processus de conditionnement. En utilisant le diagramme Yamazumi, l’entreprise a pu identifier les sources de gaspillage dans son processus, comme les attentes, les déplacements ou les surproductions.
Elle a également pu détecter les inégalités de travail entre les opérateurs qui effectuaient le même type d’opération. En appliquant des actions correctives basées sur le diagramme Yamazumi, l’entreprise a pu réduire son temps de cycle de 25%, augmenter sa capacité de production de 20%, diminuer ses coûts de production de 15%, et améliorer sa qualité et sa sécurité alimentaire. Grâce au diagramme Yamazumi, l’entreprise a pu renforcer sa compétitivité sur le marché.
Limites et défis de l’utilisation du diagramme Yamazumi
Défis de la mise en œuvre pour les grandes entreprises
Le diagramme Yamazumi est un outil simple et efficace pour optimiser la production industrielle, mais il présente aussi certains défis et limites. L’un des principaux défis est la mise en œuvre du diagramme Yamazumi pour les grandes entreprises qui ont des processus complexes, diversifiés et interdépendants. Il peut être difficile de collecter les données sur le temps de cycle de tous les postes et de toutes les tâches, de classer les tâches en fonction de leur valeur ajoutée, et d’impliquer toutes les parties prenantes dans l’analyse et l’amélioration du processus.
Il peut également être difficile de coordonner les actions correctives entre les différents postes, opérateurs ou départements, et de mesurer l’impact réel du diagramme Yamazumi sur la performance globale du processus. Pour relever ces défis, il faut utiliser des méthodes appropriées pour collecter et analyser les données, comme des logiciels ou des capteurs, impliquer les employés dans la démarche d’amélioration continue, et établir des indicateurs clés de performance pour suivre les résultats.
Limites liées à la variabilité de la production
L’autre limite du diagramme Yamazumi est qu’il ne prend pas en compte la variabilité de la production, qui peut être due à des facteurs internes ou externes au processus. Par exemple, la demande du client peut varier selon les saisons, les modes ou les événements. Les caractéristiques du produit ou du service peuvent également varier selon les spécifications, les options ou les personnalisations. La disponibilité des machines ou des opérateurs peut également varier selon les pannes, les absences ou les congés.
Ces facteurs peuvent affecter le temps de cycle des postes ou des opérateurs, et rendre le diagramme Yamazumi obsolète ou inadapté. Pour pallier cette limite, il faut adapter le diagramme Yamazumi aux conditions réelles de la production, en utilisant des données actualisées et représentatives, et en tenant compte des scénarios possibles. Il faut également réviser régulièrement le diagramme Yamazumi pour s’assurer qu’il reflète toujours la réalité du processus.
Conclusion: Pourquoi le diagramme Yamazumi est crucial pour une production industrielle optimale
Pour conclure, le diagramme Yamazumi est un outil indispensable pour l’optimisation de la production industrielle. Il permet de visualiser le temps consacré à chaque tâche dans un processus, de distinguer les activités à valeur ajoutée des activités sans valeur ajoutée, et d’identifier les sources de gaspillage et d’amélioration. Il permet également d’équilibrer le temps de cycle des postes ou des opérateurs avec le takt time, et de réduire la variabilité entre eux. Il permet ainsi d’améliorer le flux de production, de réduire les coûts, d’améliorer la qualité, d’augmenter la productivité, et de satisfaire les clients.
Le diagramme Yamazumi est utilisé dans de nombreux secteurs d’activité, comme l’industrie automobile, l’industrie agroalimentaire, ou la production en série. Il présente toutefois certains défis et limites, comme la mise en œuvre pour les grandes entreprises ou la prise en compte de la variabilité de la production. Il faut donc utiliser le diagramme Yamazumi avec rigueur et adaptabilité, et le réviser régulièrement pour s’assurer de son efficacité. Le diagramme Yamazumi est donc un outil crucial pour une production industrielle optimale.
N’hésitez pas à consulter davantage d’articles :
- Jidoka pour détecter et réagir aux écarts,
- Just-in-Time pour maîtriser sa production,
- Ou encore la boîte à outils lean.