L’AMDEC, ou Analyse des Modes de Défaillance, de leurs Effets et de leur Criticité, est une méthode systématique visant à identifier et évaluer les risques potentiels associés à un produit, un processus ou un système. Connu également sous le sigle FMEA en anglais (Failure Modes and Effects Analysis), cet outil de qualité permet d’améliorer non seulement la fiabilité et la performance d’un processus, mais aussi sa sécurité et sa durabilité.
Qu’est-ce que l’AMDEC ?
L’AMDEC est une approche proactive qui se base sur l’analyse détaillée des causes possibles de défaillance d’un produit ou d’un processus, ainsi que sur l’évaluation de leurs conséquences potentielles sur les performances, la sécurité et la satisfaction du client. Cette méthodologie implique généralement la constitution d’un groupe de travail multidisciplinaire composé d’experts métiers, d’ingénieurs et de techniciens compétents dans différents domaines concernés par l’objet à analyser.
La méthode AMDEC a pour objectif principal de :
- Identifier les modes de défaillance potentiels;
- Analyser leurs effets et conséquences sur le produit ou le procédé;
- Évaluer la criticité de chaque mode de défaillance en fonction de sa probabilité d’occurrence, de sa gravité, et de sa détection;
- Prioriser les actions correctives ou préventives nécessaires pour éliminer ou réduire les risques associés à ces défaillances.
Les différentes étapes de la méthode AMDEC
1. Formation du groupe de travail et choix de l’objet d’étude
La première étape consiste à constituer un groupe de travail multidisciplinaire, capable d’analyser en profondeur le produit, le procédé ou le système concerné. Il est également important de définir clairement l’objet d’étude, sa fonction et ses limites, afin de faciliter la compréhension et la collaboration entre les membres du groupe de travail.
2. Identification des modes de défaillance potentiels
Le groupe doit ensuite identifier les différents modes de défaillance qui peuvent affecter le bon fonctionnement du produit ou du processus. Il peut s’agir de défaillances mécaniques, électriques, électroniques, logicielles, humaines ou environnementales. Cette liste doit être aussi exhaustive que possible afin d’éviter de manquer des scénarios critiques pour l’analyse.
3. Analyse des effets et conséquences des défaillances
Pour chaque mode de défaillance identifié, il est nécessaire d’analyser ses effets potentiels sur le produit, le procédé ou le système, ainsi que sur les performances, la sécurité et la satisfaction du client. Cela permet de caractériser en détail les conséquences possibles d’une défaillance et de mieux comprendre leur impact global sur l’organisation.
4. Évaluation de la criticité des défaillances
L’étape suivante consiste à évaluer la criticité de chaque mode de défaillance, c’est-à-dire son importance relative en fonction :
- de sa probabilité d’occurrence;
- de sa gravité potentielle sur les objectifs et les exigences du produit, du procédé ou du système;
- de sa capacité à être détectée avant qu’elle ne cause de dommages ou de problèmes importants.
Cette évaluation de la criticité permet ensuite de classer les modes de défaillance selon leur priorité et de focaliser les efforts d’amélioration sur les plus critiques ou ceux qui présentent un potentiel de réduction significatif.
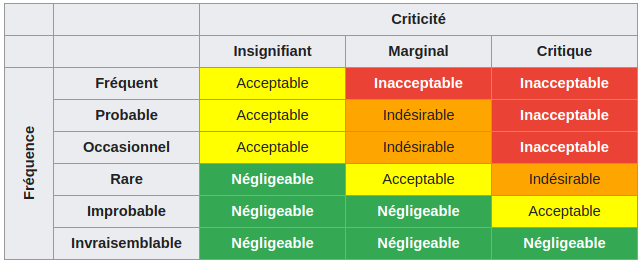
5. Définition des actions correctives ou préventives issues de l’AMDEC
Enfin, le groupe de travail doit proposer des actions correctives ou préventives pour éliminer, réduire ou atténuer les risques associés aux modes de défaillance identifiés. Ces actions peuvent inclure des modifications techniques, organisationnelles ou humaines, ainsi que des changements dans la conception, la fabrication, l’utilisation ou la maintenance du produit ou du procédé concerné.
Autres outils d’analyse de cause et de résolution de problèmes
L’AMDEC est également un outil de résolution de problèmes efficace et s’intègre parfaitement avec davantage d’outils.
Ishikawa ou AMDEC : La méthode des 5M pour une analyse de cause à effet
La méthode Ishikawa, également connue sous le nom de diagramme en arêtes de poisson ou des 5M (Matériel, Main-d’œuvre, Milieu, Méthode, Matière), est un outil efficace pour identifier les causes profondes d’un problème. Elle permet de visualiser, organiser et analyser les diverses causes potentielles d’un défaut ou d’une défaillance, offrant ainsi une vue d’ensemble claire des facteurs à adresser pour une résolution efficace.
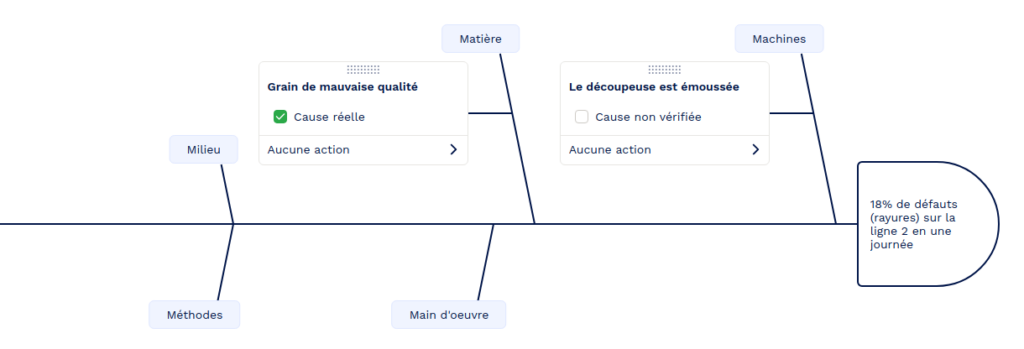
DMAIC : La structure rigoureuse pour l’amélioration des processus
Le DMAIC (Define, Measure, Analyze, Improve, Control) est une méthode structurée issue de la philosophie Six Sigma. Elle guide les entreprises à travers les étapes de définition, mesure, analyse, amélioration et contrôle, pour optimiser la performance des processus. Cette approche cible la réduction de la variabilité et l’élimination des défauts dans les processus, conduisant ainsi à une amélioration significative de la qualité et de l’efficacité.
TRIZ : L’innovation systématique pour résoudre les problèmes complexes
TRIZ est une méthode d’analyse et de résolution de problèmes basée sur l’innovation et la créativité. Acronyme de « Théorie de Résolution des Problèmes Inventifs », TRIZ repose sur l’analyse de brevets pour identifier des solutions innovantes à des problèmes techniques. Cette méthode permet d’aborder des défis complexes en identifiant et en utilisant des principes d’innovation universels, facilitant ainsi la conception de solutions créatives et efficaces.
Exemples industriels d’utilisation de l’AMDEC
L’AMDEC est largement utilisée dans divers secteurs industriels, tels que :
- l’aéronautique, où elle est appliquée pour optimiser la fiabilité et la sécurité des aéronefs et des systèmes de contrôle aérien;
- l’automobile, où elle permet d’améliorer la qualité et la durabilité des véhicules et de leurs composants;
- la pharmacie, où elle est employée pour prévenir les défaillances potentielles des procédés de fabrication et de contrôle des médicaments;
- l’énergie, où elle aide à identifier et minimiser les risques associés aux installations de production, de transport et de distribution;
- la robotique, où elle permet d’analyser l’ensemble des éléments qui composent un robot afin d’en améliorer la performance, la sécurité et la fiabilité.
Conclusion
En conclusion, l’AMDEC, avec des méthodologies complémentaires comme le diagramme d’Ishikawa et le DMAIC, offre un arsenal complet pour l’analyse et la résolution des problèmes dans un environnement industriel. Ces outils, lorsqu’ils sont appliqués de manière judicieuse et systématique, permettent non seulement d’identifier et de traiter les causes des défaillances, mais aussi de transformer les processus pour atteindre des niveaux de qualité et d’efficacité plus élevés. En fin de compte, l’adoption de ces méthodes contribue de manière significative à la compétitivité et à la pérennité des entreprises dans un marché mondial en constante évolution.